Chemistry meets sustainability: Sawdust’s sustainable transformation into bioethanol by various pretreatments method: A review
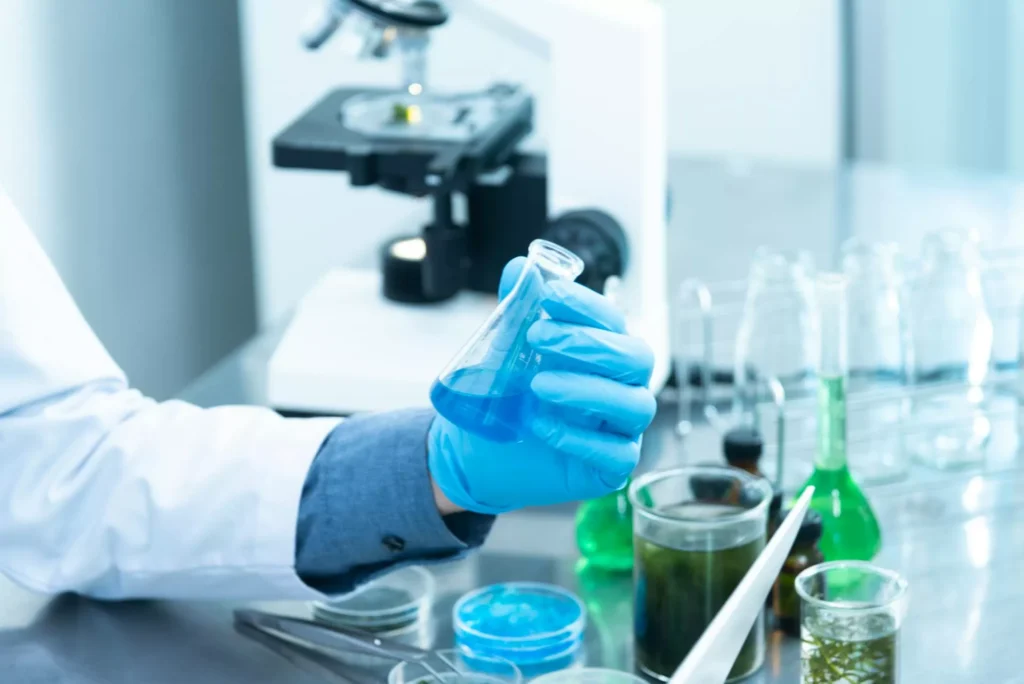
Aqsa Shahid1, Muhammad Haroon[1]*, Durdana Momin1, Kiya Hashum1, Fozia Muhammad Usman1, Zainab Ali Ahmad1, Sahid Mehmood2, Amir Zeb3
1 Department of Chemistry, University of Turbat
2 Shendong University China
3 Department of Natural and Basic Sciences, University of Turbat
Abstract:
Bioethanol is one of the most widely used biofuels and most reliable renewable fuels which can replace fossil fuels due to its high energy density, reduced carbon dioxide emissions with high air-fuel ratio, and heat of vaporization, resulting in reduced greenhouse gas emissions. Dependence on fossil fuels for energy can result in environmental damage, economic instability, and resource depletion. Therefore world needs renewable energy sources derived from biomass. Conventionally bioethanol is produced from carbohydrates in wheat and sugar cane. However, the most convenient and cost-effective method is the production of bioethanol by utilizing fragments of wood, and sawdust.
This review paper explores the transformative journey of sawdust into bioethanol with a focus on detailed current trends in pretreatment methods followed by a brief discussion on enzymatic hydrolysis, fermentation process, and distillation techniques involved. The various pretreatment methods chemical pretreatment, physical pretreatment, physiochemical pretreatment, and biological Pretreatment are discussed in detail. Each pretreatment method is discussed concerning its procedure, applications on different materials, and advantages. This comprehensive review encapsulates the chemistry behind the sustainable conversion of sawdust into bioethanol, elucidating its pivotal role in advancing renewable energy solutions.
Keywords: Biomass, pretreatment methods, biofuel, green Chemistry, sustainable energy, fermentation, hydrolysis, distillation
1 : Introduction:
A chemical substance known as “alcohol” in general refers to ethanol. Since ancient times, when it was primarily consumed as a beverage, people have used ethanol. Ethanol serves as a fuel, germicide, antifreeze, solvent, and adaptable intermediary for other organic compounds. Due to the immense benefits of ethanol, research has focused on ethanol synthesis from a variety of raw materials, which has resulted in studies on ethanol production from cellulose [1]. The most popular biofuel in use today is bioethanol, which may partially replace fossil fuels while lowering greenhouse gas emissions. Due to its high energy density, lower carbon dioxide emissions, higher air-fuel ratio, and higher heat of vaporization, bioethanol is one of the most promising renewable energies with a strong potential to replace fossil fuels [2]. Dependence on fossil fuels for energy can result in environmental damage, economic instability, and resource depletion. Due to our dependence on fossil fuels, there are now more generations of clean and renewable alternative energy sources than ever before. The Kyoto Protocol lists biodiesel, bioethanol, and biogas as examples of these alternate sources. Due to the conventional method of producing it from sucrose (sugar cane and sugar beetroot) and starch (corn and wheat), bioethanol, like other biofuels, helps to reduce pollutant emissions and reduces the greenhouse impact. The production of bioethanol from these food sources competes with the supply of food for human consumption and, in most situations, increases the cost of food and its derivatives. A long-term answer to the usage of biofuels would be [3] similar to other renewable energy sources, biomass is anticipated to become increasingly significant in the energy mix of the future [4]. A significant biomass source for biofuels and biochemicals is lignocelluloses [5]. Which is a sustainable resource and its chemical bonds store solar energy. Lignocellulose biomass (such as forestry and agricultural remains, for example, wood waste, sawdust, sugarcane bagasse, wheat straw, and corn stover) is utilized as the primary raw material employed in second-generation bioethanol production technology [6]. Though it is less expensive and more readily available than crops that produce starch (like corn) and sucrose (like sugarcane), it offers enormous potential for the manufacture of inexpensive fuel ethanol [7]. For this reason, it is thought to be less expensive than the starch-based feedstock that is currently utilized for the production of some biofuels and because it is not competitive with agro-food cultures, lignocellulosic biomass is seen as an appealing candidate for second-generation biofuel production [8]. Typically, 50–80% (dry basis) of the biomass from lignocellulosic materials is made up of polymers of 5-C and 6-C sugar units. [7]. As byproducts of agroforestry, herbaceous and woody lignocellulose are abundant, inexpensive, and highly useful biomass [6]. According to Collard and Blin (2014), lignocellulosic biomass is the dry matter of plants that is primarily made up of 25–30% hemicellulose, 40–50% cellulose, and 15–20% lignin, with smaller amounts of pectin, nitrogen compounds, and inorganic components. These materials are chained together. These days, a wide variety of lignocellulosic biomass is being studied [3]. wood sawdust contains lignocellulose components, which are composed of cellulose, hemicelluloses, and lignin. It is intriguing to consider lignocellulosic biomass as a potential source of biofuel. Because sawdust is a plentiful wood manufacturing waste, and the most reliable feedstock for processing fuels [9] [10]. The potential for lignocellulosic biomass as a source of biofuel is appealing. Wastes made of lignocellulosic materials are good, affordable feedstock for the generation of biofuel. Lignocellulosic biomass is a solid waste that may be exploited as a resource, and they don’t disrupt the food chain. Although their makeup varies greatly among the many species of biomass, they generally include 40% cellulose, 25% hemicellulose, and 15% lignin [11].
Figure 1. General composition of sawdust
Due to their plentiful availability sawdust is used as one of the most abundant feedstock for processing biofuels [9]. Saw dust is a little piece of wood that is produced during the cutting of wood. Sawdust buildup presents certain risks, including the potential for fire, air pollution, and the spread of vermin. Additionally, this waste is the perfect size for processing during the first phase of bioethanol synthesis. As a result, operations with significant energy expenditures and needs can be avoided. Sawdust and other lignocellulosic materials are primarily composed of cellulose, lignin, hemicelluloses, water, and certain salts [2]. Sawdust and other wastes, particularly those 18 from softwood, are produced in large quantities by the neighborhood’s 17 wood processing enterprises. These multi-source wastes might meet a large portion of the world’s energy demand that is still mainly met by petroleum-based goods if they were turned into biofuels. Additionally, this will open up a current chance for the forestry industry to put up with the creation of a national energy model that is dependable, sustainable, and compatible with both the energy transition strategy and the battle against climate change [8].
Table 1. Composition of lignocellulosic biomass (wood )
Lignocellulosic material | Cellulose | Hemicellulose | Lignin | References |
Hardwood | 40-55 | 24-40 | 18-25 | [12] |
Softwood | 45-50 | 25-35 | 25-35 | [12] |
Currently, the synthesis of fuels and chemicals derived from renewable raw materials, like LCB is growing interest which contributes to combat climate change and global warming, Eucalyptus, which has a high cellulose concentration (40.6-48.4%) and hemicellulose content (13.7-16% of xylan), is one of these materials. It also has a homogeneous composition. Eucalyptus wood is also one of the most prevalent types of wood in Uruguay, and its application in the creation of cellulose pulp is expanding quickly. Recently, three sawmills generated 365,000 m3 of eucalyptus timber annually, leaving behind over 40% of the wood that was processed. The major purpose of these waste products is to be utilized as fuel to produce steam and energy for operations, as well as to sell to the national electrical grid. In recent years, lignocellulosic material synthesis of bioethanol has received much research. To break down the internal structure of lignocellulosic materials and to access the sugar several pretreatments are applied. Some of the methods now in use include acid, hydrothermal, alkali, and steam explosion pretreatments [13].
This review includes a comprehensive study of different pretreatment methods such as physical, chemical, physicochemical, and biological. Moreover, this paper contains other pathways (fermentation and distillation) involved in the complete production of bioethanol from sawdust (waste).
Figure 2. Bioethanol production chain
2. The process of bioethanol production:
Various biological stages associated with the industrial transformation of lignocellulosic materials to generate bioethanol are carried out through distinct phases. Each of these processes, processes typically begins with a pretreatment stage, which can take the form of a chemical, physical, or biological treatment. This initial step involves the hydrolysis of cellulose, breaking it down into sugar monomers, which are then fermented to produce alcohol. This stage is crucial to overcoming the dense structure of the LCB, which is comprised of intricately linked elements: lignin, cellulose, and hemicellulose [14]. The transformation of lignocellulosic materials into bioethanol involves three main sequential processes: the pretreatment of raw material, the transformation of pretreated biomass into fermentable sugars via enzymatic hydrolysis, and the fermentation of these sugars into bioethanol [15]. The primary barrier to using lignocellulosic biomass for ethanol production is the protective role that lignin plays over cellulose. ; as a result, the pretreatment stage becomes particularly pivotal, since it ensures a satisfactory yield of sugars that can be fermented [3].
2.1. Pretreatment:
Pretreatment is a crucial component of workable cellulose conversion procedures [16]. Pre-treatment holds significant importance in practical cellulose conversion processes. It assumes a crucial role in the production of cellulosic ethanol by rendering the fermentable carbohydrates accessible within the material [2]. The effectiveness of pretreatment, however, relies on the specific characteristics of the feedstock being used the pretreatment phase has been acknowledged as a necessary phase [17]. Numerous pretreatment techniques have been explored in existing literature [18]. for lignocellulosic materials Break down [5]. These methods are geared towards dismantling the internal structure of these materials, facilitating access to the sugars contained in the cellulose fraction [13]. Among these, alkaline, acid, and organosolv processes stand out as the most extensively researched. These methods are geared towards dismantling the internal structure of these materials [11].
Figure 3. Various types of pretreatment
2.1.1. Chemical pretreatment:
Chemical pretreatment is the process of modifying the chemical, and physical properties of lignocellulosic biomass using chemicals like bases, acids, and ionic liquids. Because of their superior efficiency with lignocellulosic waste, chemical techniques are frequently preferred [19]. The ability of different chemicals to dissolve the dense structure of lignocellulosic biomass varies. There are different chemicals that have different abilities to disrupt the tight structure of biomass. They disrupt and dissolve the covalent bond as well as the hydrogen bond between cellulose, lignin, and hemicelluloses. Among the array of chemical pretreatment techniques accessible, two prominent methods are acid hydrolysis, alkaline, organosolvents, and ionic liquids [20].
2.1.1.1 Acid pretreatment:
Beyond 100 years, researchers have studied the utilization of acid hydrolysis to transform lignocellulosic feedstock into monomer sugars [21]. However, in recent times, the treatment of LCB with dilute sulfuric acid has been seen as the main benefit of this method [22]. The utilization of sulfuric acid for acid hydrolysis stands as the most common approach. The majority of the prior research proposes H2SO4 as a catalyst for acid hydrolysis, and it was determined that the studies have concluded that complete sugar hydrolysis (non-selective) is directly influenced by the combination of acidity and temperature. Optimal outcomes can be achieved by working at low temperatures (<50°C) with concentrated acid (30–70%) rather than dilute acid (<1%) at high heat. Among hydrolyzing acids, phosphoric acid, sulfuric acid, and hydrochloric acid are frequently employed [23]. Modifying the conditions of acid hydrolysis, such as using dilute acid under mild conditions and controlling reaction time, enables selective hemicellulose fraction hydrolysis while preserving the robust bonds within cellulose hydrolysis. The temperature for hydrolysis should be at 25℃. This hydrolysis procedure is known as acid hydrolysis [24]. Through varying concentrations and residence times, investigations reveal increased conversion probabilities of sawdust to total sugars by 50% with phosphoric acid compared to 1% v/v sulfuric acid [25].
2.1.1.2 Alkaline pretreatment:
Various fundamental pretreatment techniques employing distinct reagents have been extensively researched. Notable approaches encompass ammonia sodium hydroxide and calcium hydroxide. Among these. Moreover, NAOH’s reusability is a viable advantage in alkaline pretreatment [26]. The application of sodium hydroxide in pretreatment brings about the partial disruption of lignin-carbohydrate bonds, selective elimination of lignin and hemicellulose, structural expansion, increased surface area, and a reduction in polymerization and crystallinity [18]. Alkaline pretreatment, particularly, has been observed to diminish polymerization and cellulose crystallinity, leading to an augmented portion of amorphous cellulose nanofibrils. This alteration enhances the accessibility of enzymes to the substrate. Furthermore, alkaline pretreatment can induce the conversion of cellulose Iβ into cellulose II hydrate, characterized by an amenable structure. A commonly adopted protocol for sodium hydroxide pretreatment involves a 1% NaOH concentration, and a temperature of 60°C, [27].
2.1.1.3. Organosolv pretreatment:
Organosolv pretreatment stands out as a highly promising method for second-generation ethanol production. This technique includes the utilization of an organic liquid, such as methanol, acetone, ethanol, triethylene glycol, or ethylene glycol, along with water. Optionally, a catalyst agent like an acid or base can be added [28]. Typically, the organosolv process employs a robust inorganic acid catalyst, like sulfuric acid, which plays a key role in breaking down lignin bonds within the biomass. The main and distinctive benefit of the organosolv procedure over other chemical pretreatments is the regaining of lignin as a valuable side product. Lignon is more pure, largely unmodified, and less condensed than Kraft [29]. This process serves as both an effective biomass pretreatment to overcome recalcitrance and an efficient technique for fractionating lignin, resulting in high yields and minimal condensation products and ash [30]. Originally developed as the Alcell pulping process for hardwoods, recent studies have successfully adapted and optimized this approach for softwood, hardwood, and agricultural residue delignification. This method yields substrates that are readily hydrolyzable, with efficient glucose recovery and diminished lignin content. Notably, the recuperated lignin remains a valuable biomaterial on its own [31]. Numerous investigations have carried out organosolv pretreatment on various biomass sources like miscanthus, pitch pine, wheat straw, and olive tree trimmings [32]. Researchers have also assessed this method for the production of easily enzymatically hydrolyzable cellulosic substrates [33]. Organosolv-pretreated materials have demonstrated substantial potential for ethanol production, achieving exceptional yields of over 99.5% (36 g/L) [34]. The highest theoretical ethanol yield was attained through organosolv pretreatment with 70% sulfuric acid [35].
2.1.1.4. Ionic liquids:
Ionic liquids, regarded as potentially eco-friendly alternatives to harmful volatile organic compounds, have gained increasing attention as solvents, cosolvents, and reagents across diverse applications. Notably, their utilization extends to the pretreatment of lignocellulosic biomass for subsequent processing [36]. Over the past decade, certain ILs have proved their effectiveness in deconstructing resistant lignocellulosic biomass to yield high sugar quantities. Dialkylimidazolium-based, choline-based, and protic-acidic ILs are commonly employed for biomass pretreatment [37]. The typical procedure involves synthesizing protic ionic liquids through precise combinations of aqueous amine base and acid, followed by adjusting the water content. In delignification, the biomass is exposed to an IL solution within a vessel at elevated temperatures, which leads to the dissolution of hemicelluloses and lignin. The outcome is a cellulose-rich pulp prepared for saccharification (conversion to fermentable sugars) [38]. Specific ionic liquids like [Amim]Cl and [C2mim]OAc have demonstrated remarkable efficiency in dissolving cellulose, lignin, and hemicellulose in various lignocellulosic biomass types, encompassing corn stover, rice straw, switchgrass, and assorted softwoods and hardwoods [39]. Imidazolium-based ILs stand out for their cellulose dissolution capabilities. Out of 21 screened imidazolium-based ILs, 1-allyl-3-methyl-imidazolium chloride (AMIM-Cl) and 1-ethyl-3-methyl-imidazolium acetate (EMIM-Ac) emerged as the most efficient in dissolving cellulose and woodchips. In further studies evaluating 97 ionic liquids with varied cation moieties, AMIM-Cl, 1-butyl-3-methyl-imidazolium chloride (BMIM-Cl), and EMIM-Ac were identified one of the top solvents for cellulose and lignocelluloses [40].
Table 2. Shows the pretreatment process and its characteristic
Pretreatment processes | Acid pretreatment | Alkaline pretreatment | Organosolv pretreatment | Ionic pretreatment |
Temperature | >50 | 60 | Optimal temperature | elevated temperatures |
Concentration | 30 to 70% | 1% | 70% of catalyst | |
Theoretical yield | 50% | 99.5% | ||
Ideal reagent | Sulfuric acid | Sodium hydroxide | Organic solvent with inorganic catalyst | (AMIM-Cl) and (EMIM-Ac) |
2.1.2. Physical pretreatment:
Reducing the biomass’s particle size often involves physical pretreatment techniques [41]. Examples of physical processes include milling, grinding, mechanical extrusion [42]. as well as various forms of microwave irradiation [43] To enhance surface area and decrease the size of particles of lignocellulosic biomass, physical pretreatment methods like milling, grinding, chipping, and radiation are used [44].
2.1.2.1 Size reduction:
Size reduction is one of the most crucial initial pretreatment processes needed in the conversion of biomass to biofuel. It was found that the mechanically processed crushing technique may have had an impact on the degree of crystallinity, specific surface area of lignocellulosic biomass, polymerization, and porosity all of which add to the challenges during enzymatic hydrolysis [45]. Physical treatment of lignocellulosic biomass can open up the structure by disassembling the surface structure and reducing its size to 10 to 30 mm [46]. Grinding and milling are used for this. Mechanical pretreatment requires careful consideration of scale-up potential, operational costs, capital expenditures, and equipment depreciation [47]. The size-reduction technique of grinding increases the reactivity of biomass without generating any waste. During biomass milling, smaller wood particles will pass through a sieve, bigger ones will be recirculated and processed even more. The size of an opening on a sieve is referred to as the sieve size. The main criterion for classifying grinders is their grinding mechanism. In essence, with sharp knives, size reduction can be accomplished which splits and shear where the geometries of the particles are harmed by impact or compression [45]. Numerous studies have demonstrated that the process of decreasing particle size dimension must be carried out with caution because problems like contamination of the raw biomass and excessive heating during the grinding operation can negatively affect the material qualities exposed to grinding without changing the substance [48].
2.1.2.2. Milling:
The first stage of pretreatment is often thought of as milling. The sample is initially scaled down using cutting and milling. The ultimate particle size obtained is dependent on the kind of physical pretreatment; for instance, following milling, grinding, or chipping, the size of the particle decreases to 10-30 mm and 0.2-2 mm, respectively. High energy requirements are milling’s main disadvantage. A more sensible mechanical pretreatment in terms of energy usage is wet disk milling. However, glucose production rates Following enzymatic hydrolysis of some pretreatment lignocellulosic biomass by ball milling, and xylose are higher than under unaltered wet disk milling conditions. Sant’Ana da Silva and colleagues looked at the efficacy of wet disk milling and ball milling procedures. Their study found that the best glucose and xylose hydrolysis yields with ball milling were 78.7% and 72.1%, respectively, while the greatest glucose and xylose wet milling yields were 49.3% and 36.7%, respectively [44]. The authors’ research revealed that milling is the most widely used method (68%), followed by grinding (16%), refining (9%), ultrasonication (4%), and extrusion (3%). Furthermore, ball milling is the most common milling technique among the alternatives (65%), followed by knife milling (13%), hammer milling (9%), rod milling (7%), centrifugal milling (4%) and roll milling (2%) [49]. particle size reduction, used ball milling, jet milling, and sieve-based grindings. This process improved the substrate’s susceptibility to enzymatic degradation. In order to extract sugars from refractory oil palm mesocarp fiber. Zakaria et al. utilized wet disk milling as a secondary pretreatment method hammer milling, colloid milling, roll milling, and ball milling In the production of bioethanol, milling, and disk milling are two examples of milling types. They came to know that wet disk milling has increased the quantity of surface area that was available for the transformation of cellulose to glucose.
2.1.2.3. Grinding:
The size-reduction technique of grinding increases the reactivity of biomass without generating any waste. Grinding can alter the porosity, crystallinity, surface area, and degree of polymerization. The important factors influencing final particle size are the surrounding conditions and degree of grinding. After chipping Materials are typically 10–30 mm in size and 0.2-2 mm after milling or grinding. Vibratory ball milling outperforms traditional ball milling in terms of cellulose crystallinity and chip digestibility for (spruce) and (aspen). To reduce the size of raw materials, a variety of mechanical forces are combined, including impact, compression, friction, and shear. These forces might all coexist in a single piece of commercial machinery. In a jet mill, for example, the particles are thrown at one another Particles interact with one another in an air stream to produce strong mechanical forces. Several milling tools, such as a knife mill, hammer mill, pin mill, and centrifugal mill with a rotor, are used to break down and separate the lignocellulosic biomass [50]. Although Lignocellulosic biomass milling boosts biofuel yield, it is not a cost-effective manufacturing method due to its high energy consumption. According to a recent study, mechanical pretreatment increased the anaerobic digestion yield of biofuel by up to 22% while also accelerating the breakdown of structural materials in two independent phases [51].
2.1.2.4. Microwave pretreatment:
Electromagnetic energy waves which are known as Microwaves with frequencies and wavelengths that range from 0.3 GHz to 300 GHz and 1 m to 1 mm, respectively. For the material being heated to absorb energy, microwaves must be converted into acceptable frequencies during transmission [52]. The most popular pretreatment technique for irradiation appears to be microwave pretreatment. The application of thermal energy produced by electromagnetic radiation to substrates is how the process operates. But unlike traditional heating techniques, microwave heating is selective and only heats polar things, like water molecules, rather than non-polar ones. Due to this, water molecules vibrate extremely strongly, which causes inhomogeneity [53]. The effects of microwave irradiation on biomass and its modification have been explored since the 1960s, and in 1969 it was demonstrated and reported that microwave treatment might modify barley seeds. However, it wasn’t until the 1980s that the use of microwave irradiation on lignocellulosic biomass for improved cellulose saccharification was researched and found to be helpful in the production of biofuels. Since then, the microwave irradiation approach has been researched for processing a variety of waste types, including sludge, municipal solid waste, and biomass solid waste. It has been employed for the effective processing of biofuels [54]. Thermal and athermal actions are both included in Microwave pretreatments of materials. Two processes, namely the vibration of dipolar molecules and the motion of ions, are developed throughout this process to transfer heat. The release of extracellular and intracellular material caused by Microwave pretreatment increases a substrate’s accessibility and bioavailability. It has been demonstrated to be particularly successful in rupturing organic molecules and complicated structures. However, the precise impact of Microwave irradiation on various substrate types is still not well understood [3] and varies depending on the substrate in question as well as the temperature, power, and duration of the operation [55].
Microwave-assisted pretreatment is among the most popular procedures for Lignocellulosic biomass and operates on the principle of irradiation. This is because of the microwave’s excellent heating efficiency and straightforward operation [9]. With this approach, which has been gradually adopted from the laboratory scale to pilot one, researchers have achieved fantastic bioethanol production over 30 years. In order to enhance the use of microwave pretreatments, several studies have been carried out, including the creation of new microwave reactors and specific microwave vessels for loading biomass. In a different study, microwave pretreatment with CaCl2 boosted hemicellulose breakdown to 85.90% and specific surface area to 168.93% when compared to untreated corn Lignocellulosic biomass [56]. The benefits of microwaves include The use of renewable energy, uniform, and selective processing, and quick start-and-stop capabilities are only a few examples of technologies [57]. Microwave heating has been used to treat cellulose-containing materials [58]. The ultra-structure of starch, cellulose, and hemicellulose is modified by applying thermal and non-thermal effects to biomass via microwave irradiation. This will speed up the lignin’s rapid disintegration as well as the lignocellulosic residues’ sensitivity to enzymes [59]. Microwave pretreatment is advantageous for two reasons. The internal heating of the biomass is due to the polar bonds in the biomass and the surrounding aqueous medium vibrating as a result of the microwave radiation. The polar connections oscillate as a result of the radiation’s continually shifting magnetic field they synchronize with the magnetic field. Chemical, biological, and physical processes are accelerated by this polar bond breakdown and shock [60]. Furthermore, it is known that lignocellulosic materials heated in an aqueous media emit acetic acid, creating an acidic environment for auto-hydrolysis [61]. A variety of solvents can be employed in microwave pretreatment, however, it is well known that high boiling points, such as glycerol, tetrahydrofurfuryl alcohol ethylene glycol, and other organic molecules including ketone, dimethylsulfoxide, ethers, used in dilute concentrations [62]. The polarity orientation of the electromagnetic field will modify when the external electric current does, too. Because of their quick movement, the molecules will rub against one another. A number of chemical and physical l processes, including warming and puffing, are now completed as a result of the feedstock temperature increasing as a result of the medium’s transformation of the microwave field energy into heat energy [63]. [60] Second, it is known that when heated, lignocellulosic materials produce acetic acid, which fosters auto-hydrolysis.[61]
Microwave pretreatment in glycerol might be thought of as an excellent approach to boost the sugar yield of corncob required for the removal of alkali and alkaline metals during microwave pretreatment, as shown by Xu et al who discovered that the ethanol production was considerably raised from 26.78 to 148.93 g kg1 [64]. Another study found that microwave pretreatment with CaCl2 accelerated hemicellulose degradation to Hemicellulose degradation was accelerated by aided microwave pretreatment to 85.90% and the specific surface area to 168.93% [56]. To find practical uses for abandoned chopsticks, lignocellulosic feedstock from bode (Styrax tonkinensis) wood was subjected to microwave-assisted acid hydrolysis to yield glucose. The largest quantity of glucose produced by MW-assisted acid hydrolysis from 1 g of untreated bode wood cellulose was 0.48 g, and this resulted from heating the material at 200 °C for 1 minute while employing a catalyst containing 1.0% (w/w) sulfuric acid. However, the highest total glucose yield from the treated residue’s enzymatic hydrolysis (0.52 g) and MW-assisted acid hydrolysis (0.16 g) was 0.68 g, which was attained from a microwave heating stage. Using 1.0% (w/w) sulfuric acid as a catalyst, the temperature was 180 °C for 5 minutes. The findings demonstrated that treatment at 180 °C acted as a pretreatment for enzymatic hydrolysis of the treated residue and that treatment at 200 °C with the use of 1.0% (w/w) sulfuric acid as catalyst accelerated MW-assisted acid hydrolysis of the wood cellulose. In contrast to conventional heating, microwave irradiation shortens the reaction time and speeds up the material’s saccharification rate when heating biomass samples. The breakdown of lignocellulosic material into separate components occurs after 15 minutes of microwaving the biomass; however, prolonged heating of the sample at high catalyst concentration and temperature finally leads to the burning of the lignocellulosic material. within the biomass [65] . Chemical pretreatments assisted by microwaves have been used to successfully disrupt the refractory structures in lignocellulosic biomass. Acid- and alkali-based pretreatments have both received microwave treatment, with positive results in both cases. The success of microwave radiation has been attributed to the existence of dielectrics in biomass, such as water, cellulose, hemicellulose, and organic acids [66]. With alkaline microwave calcium hydroxide pretreatment, a maximum yield of sugar was 0.27 g/g of biomass successfully obtained at 300 W irradiation. Because glycerine and 1,4-butanediol have a high boiling point at atmospheric pressure, high boiling solvents are frequently used as part of the biomass Microwave irritation pretreatment. Lignin can be dissolved in High boiling solvents and recovered as a byproduct, while High boiling solvents microwave pretreatment can break the bonds in biomass. Therefore, if the lignin was eliminated, the residual might degrade quickly [62]. Therefore, microwave pretreatment is one of the most promising pretreatments to modify the original cellulose structure. However, To alter the original cellulose structure this process and its parameters need to be optimized [51]. However, when the cost-effectiveness of this method is taken into account, the process is quite expensive. Large microwave irradiators are necessary for large-scale pretreatment of biomass, but they are expensive, energy-intensive, and have operational limitations. Another significant drawback of the method is the high temperature and uneven heating of the biomass, which causes the production of inhibitors and, as a result, generally lower yields than one would expect [67].
2.1.2.5. Extrusion method
Extrusion is one of the physical pretreatment processes used to produce bioethanol [68]. Extrusion is a procedure in which a screw assembly is used to push equally moistened biomass material through it while applying pressure under high temperatures and at specific intervals. During this process, biomass is processed using shear forces, compression, and heat, causing physical disturbance and chemical alterations. It needs a tool called an extruder, and to improve the severity, the biomass is combined with other chemicals like sodium hydroxide, urea, or thiourea. harshness of the initial phase of treatment [69]. In this method, ingredients are heated above 300 C, then mixed and sheared, which changes the chemical and physical properties of the cellulose. The barrel temperature and screw speed are thought to cause the lignocellulosic structure to break down, shortening the fibers and producing defibrillation and fibrillation. This increases the vulnerability of the carbohydrates to enzymatic attack [70]. By coming into touch with one or two rotative screws that are inserted into a barrel or, to be more precise, an extruder. Lignocellulosic biomass is destroyed under intense shearing forces. This method is remarkably flexible, can be applied to a variety of tasks other than biomass pretreatment, and has a number of parameters that may be adjusted in accordance with the intended outcome [13]. Another benefit of extrusion is that it often has a brief residence period frequently only taking a short while [14]. Extrusion can be operated in batch, fed-batch, and continuous processing modes, and it can be done at a low temperature with little energy usage and high solid loadings. Rapid heat transfer and efficient mixing are further features of this technique. Extrusion is also a scalable technology that can yield equivalent results when scaling up from a laboratory scale to pilot and industrial stages, and it also has the potential to be combined with other pretreatment methods [15]. Since 1797, extrusion has been employed in the food, polymer, and many other industries. However, as a pretreatment method for LCB, extrusion is relatively new (the 1990s), and is gaining attention [71]. Shear forces generated by the function constantly remove the substrate’s softened surface areas and expose the interior to chemical or heat action, increasing the rate at which cellulose is converted overall. Extrusion’s appeal as a powerful pretreatment process is further increased by the large thoughts associated with it. Compared to alternative pretreatments, extrusion pretreatment provides the following benefits:
Low cost and better process monitoring and control of all variables, good adaptation to various process modifications, absence of sugar degradation products, and high continuous throughput are some of the benefits. Therefore, it appears that extrusion pretreatment is more practical for pretreating lignocellulosic biomass in order to produce bioethanol [72]. Compared to non-pretreatment material, extrusion provided active sites that were simpler to hydrolyze. However, the agent with the low-level hydrolases quantity (6.92 FPU) was able to produce more lignocellulose than was anticipated by theory. As a result, the findings indicated that the total yields of glucose and xylose were respectively 73.8% and 82.8%. Lignocellulosic biomass, at 20 FPU/g and 20% substrate loading (w/v) the final product comprising 100 g/L of fermentable sugars was produced [63]. Extrusion, diluted acid, and alkali were utilized in a comparison study of three pre-treatment methods. In which the lignocellulosic substrate used was soybean husks. In comparison to untreated substrate, it was discovered that post-pretreatment enhanced the glucose yield after enzymatic hydrolysis by 69.6%, 128.7%, and 132.2%, respectively [69]. In order to pretreat lignocellulosic biomass at higher throughput and solid levels, extrusion processing can offer an exceptional continuous reactor environment. Based on a procedure created at New York University, this alternative pre-treatment method was initially looked at for the pre-treatment of crop residues, sawdust, and municipal garbage in the 1980s. The rate of transformation of cellulose and hemicelluloses At a solid loading of 60%, the conversion rate of cellulose and hemicellulose to sugars was discovered to be around 37%. More subsequently, a similar procedure was described for the pre-treatment of sawdust with a solids loading of around 40% utilizing twin-screw extrusion and strong sulfuric acid [73].
The extrusion procedure was combined with or performed in succession with another pretreatment. For concentrated acid hydrolysis (sulfuric acid) of pine sawdust, Miller and Hester used a twin screw extruder reactor. The screw speed was controlled at 110 rpm, the barrel temperature at 60 °C, the head pressure at 780 psi, and the sawdust-to-acid ratio at 1 to 0.8. 44.4% of the sawdust solids (38.2%) were converted to soluble liquids. It was converted from cellulose to soluble mono- and oligosaccharides. Extrusion and ionic liquids, known as efficient solvents for pretreatment, have been shown through advanced research to be both environmentally friendly and inventive. Due to their excellent thermal stability, low volatility, low flammability, high ionic conductivity, and recyclability ionic liquids have been regarded as green solvents. Specifically, [EMIM]Ac is said to be thermally stable between 0 and 216°C. In addition, [EMIM]Ac is recyclable. In their 2018 study, Hamidah et al. looked into the impact of lignin on the enzymatic saccharification of recycled [EMIM] Ac. Following the third reuse, the amount of lignin in the recovered [EMIM] Ac rose with the number of recyclings, reaching 22.4%. Although the pretreated wood’s lignin content remained high, enzymatic saccharification’s ability to produce glucose was unaffected [68]. Among the benefits of this approach are its high shear, quick mixing, brief residence time, moderate barrel temperature, lack of furfural and HMF formation, lack of washing and conditioning, capacity to respond to process modification, simplicity of scale-up, and most notably, potential for continuous operation. Extrusion also causes no effluent, which eliminates the need for expensive effluent disposal and solid waste generation. In order to obtain 94.8% glucose conversion following enzymatic hydrolysis (glucose yield of 0.37 g/g biomass) [44].
Table 2. Wood material pretreatments and their glucose yield:
Pretreatment type | Raw material | Conditions | Total glucose yield | References |
Microwave | Beech wood | Treated at 180c for 30 min with ammonium molybdate | 59.5% | [67] |
Extrusion | Pinewood | 180c screw speed at 150rpm | 65.8% | [74] |
Microwave | Eucalyptus sawdust | Treated at 180c for 30 min | 104.4 | [63] |
Acid pretreatment | Pine sawdust | Treated with H2So4 at 130c For 25 min | 50% | [72] |
2.1.3. Physiochemical pretreatment:
Physicochemical procedures are those pretreatments that bring together chemical and physical elements [75]. These processes include wet oxidation, liquid hot water (LHW), ammonia fiber explosion (AFEX), CO2 explosion, and steam explosion [76]. are the most efficient and eco-friendly ones that are currently accessible. They’ve undergone pilot-scale testing for industrial applications and were optimized for a broad range of feedstock [77].
2.1.3.1. Steam explosion:
pretreatment that allows the interruption of lignocellulosic biomass structural constituents via heating, production of organic acids(acetic acid) throughout the process, and cutting forces subsequent to the extension of moisture [78, 79]. This procedure is said to be the best and has been proven to be effective in enhancing the anaerobic biodegradability of several organic wastes, such as animal by-products, sewage sludge, microalgae, and lignocellulose biomass [80]. Furthermore, among the previously described pretreatments, (SE) is thought to be one of the highly economical, beneficial, and ecologically friendly, hence it is being thoroughly studied at the flier-to-commercial scale for a variety of lignocellulosic biomaterials [81]. The hydrolysis of glycosidic linkages in the hemicelluloses and, to a lesser extent, in the cellulose, is often the outcome of the steam explosion process. Additionally, it causes the hemicellulose–lignin linkages to split. The processes cause lignin to become more soluble in alkaline or organic solvents and enhance the solubility of hemicelluloses in water, leaving cellulose as a solid junk with a decreased extent of polymerization (DP) [82]. When comparing steam explosion techniques to alternative pre-treatment methods for the chemical lignocellulose utilization process, the general benefits are as follows: The only chemical used is water. high hemicellulose yield and low degradation byproducts When compared to acid hydrolysis operations, the mild pH of reaction media results in less equipment corrosion. Acid recycling and handling stages are avoided, and the explosion effect causes the solid wastes to break down into individual fibers from bundles [83].
2.1.3.1.1. Procedure of the process:
There are two separate phases in the SE pretreatment process. There is a boiling phase of steam and an explosion phase. The initial phase of this process involves temperatures between 170° and 210°C to induce the hydrolytic breakdown of the LC matrix. The process’s second phase is the transformation of thermal energy into mechanical energy [84]. For a brief period of time (minutes), the biomass is subjected to high-pressure saturated steam, and the pressure is then quickly withdrawn [85]. Biomass is treated in hot, compressed vapor during this pretreatment procedure. The substrate then undergoes an explosive breakdown when the pressure is abruptly reduced. When pretreated at a temperature above 150 °C and a pressure of approximately 1.03 × 106 Pa, the substrate biomass would yield many more benefits than raw biomass. These benefits would include sufficient disruption of the carbohydrate linkage through hemicellulose hydrolysis, improved lignin and cellulose crystallinity and thermal stability, and a decrease in the samples’ alkali ion content [86]. Through the opening of the wood structure, the SE raises the porosity. the impact of SE on poplar wood’s pore size and enzymatic hydrolysis, and it was found that SE raises porosity and helps produce higher glucose yields. SE and acid pre hydrolysis’s effects on enzymatic hydrolysis [87]. Based on a factorial design generated using SAS Institute Inc.’s JMP software in Cary, NC, USA, the temperature and retention time were predicted to be 210 °C and 15 min, respectively, to provide the maximum yields of glucose and xylose following enzymatic hydrolysis. A severity factor (SF) of 4.4 was obtained by combining those characteristics into a single one, the severity factor [88],[89],[90]. The severity factor (log RO) is frequently utilized to examine the efficaciousness of pretreatments carried out under various experimental circumstances and to predict outcomes. Based on the Arrhenius Law, this component is equivalent to the logarithm of the reaction ordinate (RO), which integrates pretreatment temperature and residence time in one parameter.
The impact of acid catalysis can be taken into account by extending Eq. 1 by including the pretreatment pH as indicated by the combined severity factor (CSF) (Eq. 2).
Where T is the pretreatment temperature in °C and t is the time of pretreatment in minutes in both scenarios. For many years, log RO and CSF have been extensively utilized to directly compare the outcomes of biomass pretreatments carried out under various experimental setups [91].
2.1.3.1.2. Application of SE pretreatment on various materials:
Throughout steam-explosion pretreatment of aspen wood, a study of material equilibriums for pentosan, hexosan, and lignin revealed nearly measurable regaining of cellulose in the water-insoluble portion. In contrast to unwanted pyrolysis, diluted acid impregnation led to more selective hydrolysis of pentosan and provided a further reachable substrate for enzymatic hydrolysis [92]. According to another study, when pine is subjected to steam explosion treatment, variations in brightness and color components may be easily noticed, resulting in the development of goods that are dark and brownish. The color ratios of the red, blue, and green components in the pine samples following pretreatment are less than those of the untreated pine. [93]. Furthermore, a separate study documented the pretreatment of hardwood and softwood using steam explosion. The wood chips, comprising 44 hardwood species and 6 softwood species, were treated with saturated steam at 180°C for 15 minutes and then fiberized for 1 minute in a defibrillator. After a sample of the acquired fiber was hydrolyzed with the enzyme without any extraction, a hydrolyzate was produced that was primarily composed of 30–40% xylose and 50–60% glucose. Depending on the species, the amount of enzymatic hydrolysis of the remaining polysaccharides in the fiber ranged from 80 to 17% [94]. For different wood materials, the early rate of hydrolysis using Trichoderma reesei cellulase is directly related to the outward area that the enzyme has access to. Both autohydrolysis in a steam exploder and diluted acid hydrolysis in a continuous flow reactor are comparable pretreatment techniques because they improve the wood’s pore volume by eliminating hemicellulose, which increases the surface area of the enzyme [95]. Pretreatment is thought to have its primary effect from increasing the amount of pore surface area that is available for enzyme molecules to occupy. Measurements shown by a study indicate a significant increase in the pore capacity accessible to solute probes measuring 5–9 nm. The pretreated wood that was later baked in an oven had inadequate hydrolysis and reduced accessible pore volume. During pretreatment, xylans are easily hydrolyzed to xylose, and as reaction conditions become more severe, the quantity of xylose present in the solution following steam pretreatment reduces due to decomposition [96]. In a study, Salix wood chips were heated at a rate of 10 K/min by thermogravimetric analyzers (TGAs) and subsequently treated by SE under various pretreatment settings to analyze the pyrolysis characteristics. The SE pretreatment changed the structure of the biomass as well as its pyrolysis properties. The depolymerization brought on by the SE pretreatment caused the hemicellulose decomposition area to shift to a lower temperature range. Peak cellulose intensities rose under severe pretreatment conditions and fell under mild ones. The SE pretreatment also raised lignin reactivity. However, because of condensation and re-polymerization reactions, harsh pretreatment conditions led to a decrease in lignin reactivity [97].
2.1.3.2. Liquid hot water:
Since water, which has a pH of neutral, is utilized as the pretreatment medium, the liquid hot water (LHW) pretreatment is typically recognized as the neutral pretreatment [98]. One hydrothermal pretreatment technique used for lignocellulosic material pretreatment since several decades ago, for example, in the pulp industry, is cooking the material in liquid hot water (LHW). High-pressure water can permeate the biomass, hydrate the cellulose, and extract some of the lignin and Hemicellulose [75]. Liquid hot water (LHW) biomass pretreatments are found to produce less waste and inhibitory products and to release less pollutants than other hydrothermal pretreatment methods currently in use. Additionally, they require less energy and chemical inputs and are less expensive in terms of capital investments [99][3].
2.1.3.2.1. Procedure of the process:
This approach| `h increases the breakdown of the lignocellulosic matrix at a temperature of 160–240 degrees Celsius by applying hot water under high pressure while keeping it liquid [56]. The hydrolysis of cellulose, the majority of hemicelluloses, and a small amount of lignin is catalyzed by the liberated hydronium ions. The breakdown of hemicellulose in LHW can be broadly categorized into three stages: the production of primary products through reactions on the biomass’s surface, the dissolving of primary products in water, and the subsequent breakdown of the primary products. Consider sweet sorghum bagasse (SSB). After being separated and hydrolyzed, the majority of hemicellulose fractions become derivative oligomers or monomer sugars, which can be utilized as substrates to create a variety of biological substances, including succinic acid [100]. Both batch reactors and flow-through reactors can be used for LHW pretreatment. Water slurry and biomass are heated in batch reactors to the appropriate temperature and maintained at pretreatment settings for the intended residence time beforehand being chilled. Hot water is forced over a stationary bed of lignocelluloses in a flow-through reactor. For the removal of hemicellulose, the flow-through method is generally thought to be superior to the batch method. This is partially due to the fact that a flow-through reactor’s high volume of water rapidly dilutes and eliminates organic acids, lowering their concentrations and shortening the amount of time they have to work on the solid hemicelluloses [98].
2.1.3.2.2. Application of liquid hot water treatment on various materials:
Furthermore, it was shown that hydrothermal pretreatment at 150–180°C caused the crystalline structure of bamboo cellulose to degrade and convert to Iβ. Liquid hot water pretreatment at 200°C increased the glucose yield by 3.8 times through enzymatic hydrolysis. Moreover, at high pretreatment temperatures, the water’s pH sharply dropped and more carbohydrate breakdown was introduced. stronger LHW pretreatment severity has also been linked to a stronger lignin-enzyme binding ability, according to several reports [101],[76].
Additionally, an investigation found that the existence of acid catalysts enhanced the efficiency of digestion; sulfuric acid, in particular, is the most commonly employed acid and has a very strong hemicellulose extraction. keeping glucan content, increasing the production of sugar for following hydrolysis, protecting soluble sugars, reducing the production of byproducts that impede consequent hydrolysis and fermentation method, and being profitable are all goals that an efficient LHW pretreatment should achieve [100]. A recent study aimed at improving the enzymatic hydrolysis of Populus tomentosa, researchers employed a novel two-step pretreatment approach involving fungal treatment in conjunction with liquid hot water (LHW) treatment. The findings revealed that as the temperature increased, both lignin and cellulose content rose, whereas a substantial portion of hemicellulose underwent degradation throughout the LHW pretreatment. Notably, the greatest elimination of hemicellulose, reaching 92.33%, was achieved when combining Lenzites betulina C5617 with LHW treatment at 200 °C—almost double the efficiency of sole LHW treatment at the same temperature. Saccharification of poplar co–treated with L. betulina C5617 and LHW at 200 °C exhibited a remarkable 2.66-fold increase in glucose yield compared to the solo LHW treatment. Additionally, a 2.25-fold increase in glucose yield was attained through the combination of Trametes ochracea C6888 with LHW. This dual treatment strategy proved effective in accelerating the enzymatic breakdown of poplar wood [102]. a separate investigation focusing on the part of lignin in predigested hardwood, the study revealed that as the intensity of LHW pretreatment heightened, cellulose hydrolysis amounts actually decreased. Residual solids from hardwood processed in association with liquid hot water at different severities (ranging from log Ro = 8.25 to 12.51) demonstrated substantial recovery of 80 to 90% of the original lignin. Concurrently, the proportion of acid undissolve lignin (AIL) to acid dissolve lignin (ASL) enhanced, and spherical lignin droplets formed on the surface of cell wall —a phenomenon consistent with previous literature. The researchers utilized the glass transition temperature (Tg) to characterize the extracted lignins, discovering that as severity was increased from log Ro = 10.44 to 12.51, the Tg of extracted lignins rose from 171 to 180°C. This Tg elevation indicated condensation processes in lignin molecules during pretreatment, leading to structural changes in the lignin
[103] [103]. In the current work, Italian green peppers were subjected to an LHW pretreatment for 40 minutes at 180 °C in order to measure glucose yields. A worldwide glucose yield of 61.02% was attained under these circumstances. Furthermore, the liquid fraction from enzymatic hydrolysis contained very low amounts of phenolic compounds (range from 69.12 to 82.24 mg/L), which lessened the liklelihood that these components would hinder fermentation. The findings indicated that Italian green pepper is a promising feedstock for obtaining free sugars and reducing the massive amount of food waste that is thrown away each year.Predigested olive tree pruning biomass can be utilised as a starting point for enzymatic hydrolysis at high level substrate concentrations (≥20%), according to a different study [104]. After LHW-pretreated solids are saccharified by enzymes at a consistency of 20%, a glucose solution containing 52 g/L and a 64% enzymatic hydrolysis yield is obtained. The amount of glucose is boosted by a delignification process applied to pretreated materials [105]. A study focused on pine, grapevine, and poplar aimed to identify optimal conditions for hemicellulose recovery through pretreatment. The experiments were performed in a batch-mode, high-pressure reactor with self generated pressure, employing a liquid-to-solid ratio (LSR) of 15, and varying temperatures (170–220 °C) and durations (15–180 min). Across the different biomass species, the highest hemicellulose recovery in liquid products—approximately 60%—was attained at mild treatment severities (log Ro = 3.8–4.1), resulting in 70%–85% hemicellulose removal. In the entire scope of pretreatment severities, the generation of key degradation products, including acids (formic and levulinic acid) and furans (furfural and HMF), remained relatively low, at or below 1 mg/mL.Under the most severe hydrothermal pretreatment conditions (log Ro = 4.7), enzymatic hydrolysis of the original lignocellulosic biomass to glucose was notably limited, with only a 10% conversion observed. This low conversion persisted for pretreated pine biomass (16%). However, a significant improvement was evident for poplar (49%) and particularly for grapevine (77%). These results highlight the influence of treatment severity on hemicellulose recovery and subsequent enzymatic hydrolysis efficiency, with milder conditions proving more favorable for optimal outcomes [106].
2.1.3.3. Ammonia fiber explosion:
Ammonia is a potent pretreatment reagent that can cause the biomass of lignocellulosic materials to expand. Ammonia, an alkaline substance, functions by dissolving cellulose’s crystallinity and acetyl bonds found in the lignocellulosic biomass’s chemical structure [107]. There is a description of various ammonia pretreatment methods, including ammonia fibre explosion, low-liquid ammonia treatment, and ammonia recycling percolation, and soaking in aqueous ammonia. Among them [108]. Volatile ammonia serves as the primary reactant in the thermochemical preparation known as “ammonia fibre expansion” (AFEX), which is applied to cellulosic biomass. In order to improve biologically-catalyzed pretreatment biomass breakdown into fermentable sugars and to economically lessen the recalcitrance of lignocellulosic biomass, Bruce Dale initially developed this procedure. AFEX is a dry-to-dry method that cannot remarkablely change the structure of biomass, unlike the majority of conventional aqueous-based thermochemical pretreatments. It also eliminates the need for a washing phase, which is costly and generates trash [109]. The AFEX process produces a nearly full solid recovery yield by changing the feedstock’s structural and molecular characteristics without producing liquid dissolved fractions from the feedstock [110]. It has been shown on a small scale that ammonia fibre explosion (AFEX) can overcome biomass recalcitrance for the generation of cellulosic ethanol [111]. To lessen biomass’s resistance to hydrolytic enzymes, the AFEX method combines a chemical (ammonia) and physical (high pressure and temperature) action. It is normally possible to adjust parameters such ammonia loading, reaction temperature, water loading, and residence length to optimise the ammonia fibre explosion pretreatment However, moderate ammonia concentrations (40–80%) are commonly used while doing the traditional AFEX process [85].
2.1.3.3.1. Procedure of the process:
Throughout AFEX, biomass and liquid anhydrous ammonia are in contact with one another for a brief amount of time (5–60 minutes) at approximately low temperatures (60–100) and pressures (1.7–2.1 MPa) while experiencing different water loadings [112]. Following the quick release of pressure, the ammonia gas expands quickly, causing swelling and the physical disruption of biomass fibres. Furthermore, roughly 95% of the ammonia can be achieved and recycled in the gas phase, with the remaining ammonia in the lignocellulosics possibly providing a source of nitrogen for the microorganisms during fermentation [113]. During AFEX, ammonolytic breakage of cell wall ester linkages produced acetamide (25 mg/g AFEX CS) and many phenolic amides (15 mg/g AFEX CS), which are nutritious for fermentation that occurs later on [114]. According to reports, AFEX pre-treatment produces 36 times fewer furans and 100–1000 times fewer carboxylic acids than dilute acid pre-treatment [115]. Inhibitors generation is insignificant in this scenario. Among the many benefits of this technology are (a) the absence of harmful compounds created during the process, increased synthesis of enzymes (such cellulase), and large surface area [116].
2.1.3.3.2. Application of AFEX on various materials:
In one study, LMAA pretreatment was applied to distillers’ dried grains with solubles (DDGS), corn fiber (CF) ,corn gluten feed (CGF) and oil palm frond (OPF) at different moisture percentages. The specific ammonia loading rate, one hour of ammoniation, and an incubation temperature of 75°C were all taken into consideration. For the majority of the materials studied, this pretreatment effectively raised the materials’ percentage of α-cellulose, reduced their lignin content, and enhanced their enzymatic digestibility. It was discovered that the impact of moisture content (30 and 50% db) outweighed the impact of incubation period (24 and 72 hours) [117].
Reports are provided on the results of pretreating switch grass using ammonia fiber explosion (AFEX) utilizing its primary process variables. A reactor temperature of around 100°C and an ammonia loading of 1:1 kg of ammonia: kg of dry matter with 80% moisture content (dry weight basis [dwb]) for five minutes of residence time were determined to be the ideal pretreatment conditions for switchgrass. The findings of hydrolysis for samples subjected with AFEX and those not indicated a glucan conversion of 93% and 16%, respectively. Approximately 0.2 g ethanol/g dehydrated biomass was the measured ethanol yield of the optimized AFEX-treated switchgrass, 2.5 times higher over untreated sample [118].When pretreatment conditions are identical, the total yield of fermentable sugars obtained by the enzymatic hydrolysis of maize stover prepared utilizing the laboratory-scale AFEX method is similar to that of the pilot-scale AFEX process.A comprehensive standard operating process for the safe and reliable operation of laboratory-scale reactors utilized for lignocellulosic biomass AFEX processing [109]. The enzyme hydrolysis of the AFEX treated corn stover and the fermentation showed that AFEX pretreatment is an effective pretreatment. Both the rate and extent of glucose, as well as xylose, is significantly higher in AFEX subjected sample co relate to the untreated sample. It is clear that all pretreatment parameters (such as moisture, temperature, treatment time, ammonia loading, etc.) affect the reactivation of treated biomass [119]. A laboratory-scale (5 L) packed-bed ammonia fiber expansion (AFEX) reactor system’s performance was previously reported, and it demonstrated great potencial for biomass pretreatment at dispersed depots.,They report on the execution of a pilot-scale packed-bed AFEX reactor system that is 90 times larger. Above a 5-year time of period, the system produced over 1,500 batches (~36 tons) of pretreated crop remaining. 76% of the ammonia was recycled and used again after almost all of the unreacted ammonia was effectively released out of the biomass. Pilot-scale pretreatment performance was similar to laboratory-scale results, with an average yield of 74% glucose and 75% xylose in a standard test, as opposed to 71% and 73%, respectively [120].
2.1.4. Supercritical fluids:
When a fluid is below the pressure required for condensation and higher than the critical temperature and pressure (Tc and PC), it is referred to as supercritical. According to Himmelblau, “the set of physical circumstances wherein the density and some other properties of the liquid and vapour become similar is the critical phase for the gas-liquid transition.” The critical point is reached when the liquid and gas states coexist and become identical at supercritical conditions. The concepts of “green chemistry” are very popular these days. Of particular importance include substituting safer chemicals or solvents (such CO2) for common solvents and using renewable feedstocks to make processes more environmentally friendly.More than 150 years later, Zosel (1978) employed supercritical carbon dioxide (scCO2) to isolate caffeine within coffee beans, marking the first technological use of a supercritical fluid [121],[122]. Supercritical water is said to be helpful for gasification and hydrolysis when it comes to cellulose. Supercritical methanol has been used to create CA fibres, and supercritical ammonia has been used to turn cellulose into crystals. Using sc-CO2 drying, nanoporous cellulose aerogels were produced. Supercritical CO2 was utilized for the acetylation of Hanji, as a reaction medium a traditional Korean cellulose textile, for improving its water repellency and to maintain its other qualities [123],[124] .
2.1.4.1. Carbon dioxide explosion:
Large-scale industrial sources, such as steel mills, fossil fuel power plants, and building cement manufacturers, emit CO2. It is also easily available as a byproduct of refineries’ production of ethanol, natural gas, and ammonia. [125]. To boost cellulose’s reactivity, supercritical carbon dioxide is used to cellulose-containing polymers [123]. The usage of SC-CO2, one of these supercritical solvents, has drawn the most interest because of its remarkable qualities, including its designation as a “Clean and Green” solvent. It is not reactive by nature, less viscous, less polar, non-toxic, and promotes mass diffusion. It is also non-flammable. It reduces the down-streaming process since it is simple to remove from the reaction media by depressurization [124]. Therefore to increase the cellulose hydrolysis’s pace and extent. Cellulosic materials include recycled paper mix, Avicel, sugarcane bagasse, and reclaimed paper residue that is being repulped are put in a reactor with pressurised carbon dioxide during this pretreatment process [123].
According to the authors, pretreating wood with supercritical CO2 enhanced its water permeability by removing chemicals that impeded permeation [126].
The dimensions of carbon dioxide molecules are similar to those of water and ammonia, and they can enter the feedstock’s pores. Additionally, the breakdown of the cellulose structure made possible by the explosive release of carbon dioxide pressure increases the substrate’s surface area that is available for enzymatic hydrolysis. Enzymatic digestibility can be effectively increased with supercritical CO2 [127]. In industrial reactors, the critical temperature (T c) and pressure (P c) of CO2 (30.95°C and 72.8 atm) are easily reached. Since CO2 is non-flammable and is produced when organic material completely oxidises, it can be used as a safe, inert solvent in oxidation and other reactions where hydrogen and oxygen are required to react, including the creation of hydrogen peroxide
2.1.4.1.1 Application of carbon dioxide on various materials:
Investigation on supercritical CO2 treatment of wood is being applied to the following areas: preservative treatment of wood-based composites, elimination of heavy metals out of wood treated by chromated copper arsenate (CCA), and selective extraction of wood’s valuable chemical components.16–17 According to the authors, pretreating wood with supercritical CO2 enhanced its water permeability by removing chemicals that impeded permeation[122]. Supercritical carbon dioxide is ideal for this kind of process because it is entirely miscible with the majority of organic solvents. A noteworthy impregnation loading was accomplished by using supercritical carbon dioxide as a carrier solvent for the siloxane modification reagent. A WPG of up to 63% (wt) was detected utilizing the relative extension in sample mass before to and following impregnation [128]. A study demonstrate that solid wood dyeing is significantly improved by water-saturation of supercritical carbon dioxide (scCO2), a reliable green dyeing medium. Three European hardwood species—beech (Fagus sylvatica) and disperse blue 134 oak (Quercus robur), and birch (Betula pendula)—have been shown to exhibit this. Adjusting the dyeing temperature between 45 and 100 °C and the pressure between 10 and 30.0 MPa showed that the ideal combination of parameters was 20.0 MPa and 100 °C [129].
A study Investigated the properties of niosomes made using a brand-new supercritical carbon dioxide fluid (scCO2) process .The niosomes produced via the scCO2 approach about 10% (w/w) ethanol had a greater trapping effectiveness (12.22 ± 0.26%) compared to those produced through the scCO2 process in the absence of ethanol (8.40 ± 1.60%) and by the traditional chloroform film process with sonication (10.85 ± 0.24%). With and without ethanol, niosomes produced using the scCO2 technique had enormous unilamellar structures under TEM, with average diameters of 202.5 ± 136.7 nm and 271.9 ± 159.6 nm, respectively [130]. In another study, an orthogonal cutting process was used to conduct an experiment comparing the effectiveness of the SCCO2 and MQL techniques in terms of tool-chip, chip thickness contact length, cutting temperature, and cutting force. By comparison to MQL machining technique, the experimental findings demonstrated that the use of SCCO2 as the cutting fluid resulted in lower cutting temperatures, cutting forces, chip thickness, tool-chip contact lengths, and specific energy pressure [131]. Another the current study examined the fundamental justifications for use of supercritical carbon dioxide fluid in cleaners with regard to wool’s thermal properties, chemical and crystal structures, macrochain conformations, and surface morphology. Analysis shows that wool subjected at various pressures in supercritical CO2 fluid has improved crystallization in both the α-helix and β-sheet structures. In addition, the supercritical treatment caused the crystals in wool fiber to enlarge and reconsolidate. The FT-IR analysis reveals that during the supercritical treatment, stronger hydrogen bond interactions were formed between the wool’s macromolecular chains. This was accompanied by a notable change in the structure from α-helix to β-sheet, as well as an acidic hydrolysis or oxidation of disulfide bonds in the wool scales[132].
2.1.5. BIOLOGICAL PRETREATMENT:
The present tendency is to employ fermentation to turn less usable material into high-quality biofuel or simpler byproducts [133]. By doing this, we may produce renewable fuels and become less dependent on finite fossil fuels. This is significant because biofuels of this kind are long-term and will support future generations. AFEX, alkali, diluted acid, ozonolysis, milling, liquid hot water, CO2 explosion, steam explosion, wet oxidation, and biological pretreatment are some of the pretreatment methods utilised before the actual fermentation to convert biomass [70]. An important step in turning lignocellulosic biomass into bioethanol is pretreatment. Biological pretreatment appears to be the most promising of the pretreatments discussed above because it is an environmentally benign technique and doesn’t produce any inhibitors. The use of a natural microorganism’s metabolite in biological pretreatment to produce ethanol from biomass is a promising technique because it offers a number of benefits, including an environmentally and financially feasible method of increasing the rate of enzymatic saccharification. This procedure doesn’t release any hazardous substances into the environment and doesn’t require the recycling of chemicals because none were used in it. The efficient breakdown of lignocellulosic biomass occurs when a diverse range of bacteria and fungi work together to form a microbial consortium [134].
2.1.5.1.Microorganisms used in biological pretreatment:
Enzymes play a major role in biological pretreatments, implying that the microbe responsible for manufacturing the relevant enzymes is important [4]. Using the optimum microorganism to convert raw materials into the finished product or biofuel might increase production in an economical manner. A systematic thoughtful of the microorganisms Taking part in the transformation may improve it. Pretreatments with biological agents are required because they improve the rate of fermentation or digestibility. Numerous bacteria, including Bacillus and Actinomycetes as well as several recognised fungus, are capable of breaking down organic materials, according to past study conducted by various scientists and documented in papers and reports [135]. [6] demonstrated the broad-spectrum biodegradation of microbial consortia made up of Aspergillus, Candida, Streptomyces, and cellulolytic bacteria from the family Bacillus. Numerous enzymes are involved in the degradation of complex macromolecules, such as amylase, xylanase, cellulase, and cellobiase. Polysaccharides are broken down into sugars by cellulase, proteins into amino acids by protease, and lipids into long chain fatty acids and glycerol by lipase [136],[137]. Lignin has a strong resistance to breaking down. Before fermentation, Aspergillus niger is used to biologically pretreat lignocellulosic Azolla, which has around 15% cellulose, to make bioethanol [138]. Fungi facilitate simultaneous fermentation and saccharification, which can enhance ethanol production [10]. By the aid of brown, white, and soft-rot fungi like Gloeophyllum trabeum, P. chrysosporium, and Trichoderma reesei, mild alkali and steam pretreatment of wet-milled maize fibre are evaluated. When hydrolysates are fermented immediately into ethanol, the yields of ethanol produced are 75% more than when a commercial cellulase enzyme is employed for saccharification and fermentation at the same time [11]. When compared to traditional physicochemical approaches, which demand significant energy inputs, this biomass pretreatment procedure is thought to be more effective and environmentally friendly[12]. Numerous white rot fungi, including Pleurotus ostreaus, P. chrysoporium, Ceriporia lancerata, Cyathus stercolerus, and P. chrysoporium, have also been shown to have the capacity to manufacture lignin-degrading enzymes that effectively delignify a variety of lignocellulosic biomasses [2, 13]. According to reports, pretreating sweet chestnut leaves with the wood-decaying fungus Auricularia auricular-judae enhanced the biogas output by up to 15% when compared to the untreated state [14]. Cyanthus stercoreus and Trametes hirsute pretreatment of cedar wood chips resulted in increased product production, including biomethane [15]. As a result of their adaptation to pH and temperature fluctuations, consortia of various microbes are more resistant to substances that might hinder growth, like heavy metals, hazardous substances, or pollution [5]. Potential consortia that are able to break down lignocelluloses include microorganisms that have been isolated and identified from various ecological niches, example manure, soil, animal rumen or agricultural leftovers [5]. Since microbial consortia are important in pretreatment, it is important to understand the individual organisms involved in forming a particular consortium for the particular biomass to be treated. This knowledge may result in a significant shift in the rate at which biofuels are produced with high quality. Moreover, this can assist in resolving the energy problem that humanity is now experiencing [16].
2.1.5.2. Factors affecting biological pretreatment:
Numerous elements influence a biological pretreatment’s efficacy. This comprises elements relating to the substrate, such as biomass composition, in addition to features like inoculum concentration, aeration rate, moisture content, incubation period, incubation temperature, pH, and kind of microbe involved. The biomass’s makeup changes according to species and variation. For the purpose of effectively removing hemicellulose and lignin stream from the biomass, an suitable microbial consortia necessity employed, depending on the makeup of the particular biomass. The ideal temperature, pH, and duration of incubation differ depending on the microbial consortia that is being employed for biological pretreatment. The dispersion of volatile chemicals created during metabolism, humidity management, heat dissipation, oxygenation, and CO2 elimination are all facilitated by aeration. [139].
2.1.5.3.Advantages of biological pretreatment:
Typically, enzyme cocktails or direct microbial growth on the feedstocks are used in biological pretreatments. This pretreatment method is low severity, selective, and requires little energy or chemical addition. Since biological pretreatment is carried out at mild circumstances, among the most significant environmental profits is that the byproduct formed in the pretreatment does not prevent future fermentation or hydrolysis. There is no need for chemical recycling, it is a chemical-free process, and no poisonous or dangerous substances are released into the environment. [140].
Table.3.The disadvantages and advantages of pretreatment methods
Pretreatment methods | Advantages | Disadvantages | References |
Acid pretreatment | fractionation of hemicelluloses and lignin Enzymtic hydrolyses sometime not required due to acid hydrolysis | Harmful by products High cost | [63] [69] |
Alkaline | hemicellulose and lignin are removed /hydrolysis Increases surface area | calcium and magnesium salts are formed | [67] [141] |
Ionic liquids | cellulose is seprated from lignocellulose | High cost | [63] [142] |
Organosolv | Pure lignin is obtained, and used as value added products | Solvents inhibits enzymtic hydrolysis /costly | [67] [63] |
Extrusion | Shortening of fiber Less inhibitory compounds are produced | Highly time consuming /high cost | [20] [69] [74] |
Microwave | Cheap methode Generates less pollution | Carbohydrates are degraded at higher temperature Lack of large scale equipment | [20] [67] [63] |
particle size is reduced and crystallinity of Lignocellulosic material | High energy consumption | [69] | |
Steam explosion | Causes lignin and hemicelluloses to split | Requires energy, High cost | [82] |
Liquid Hot water | Less inhibitory compound,less expensive and require less energy | Time consuming | [99] |
CO2 Explosion | Increases the cellulose hydrolysis’s pace and extent. | High cost | [123]. |
AFEX | High glucose yield production, less inhibitory compounds | High cost | [111] |
Biological | low severity, selective, and requires little energy or chemical addition. | Requires suitable tempreture and PH | [140] |
2.2. Enzymatic hydrolyses:
Enzymatic hydrolysis of lignocellulosic biomass is a promising method due to its fractionation capabilities and the enzymes’ remarkable specificity in breaking down polysaccharides like hemicellulose and cellulose into valuable sugars like glucose and xylose [143]. When cellulose is subjected to the mild circumstances of pH between 4.5 and 5 and temperature between 40 and 50 °C, glucose is produced by the action of the cellulose enzyme. Deodar sawdust, also known as Cedrus deodara, underwent thermochemical pretreatment, enzymatic hydrolysis, and fermentation to produce bioethanol. Biomass pretreatment Due to its effect on fractionation and the great selectivity of enzymes hydrolysis during the alteration of lignocellulosic biomaterial to fermentable sugars is intricate because of the interplay between substrate-related and enzyme-related factors for the hydrolysis of polysaccharides (and hemicelluloses and cellulose) to sugars (such as xylose and glucose) To illustrate, consider the case of Cedrus deodara (deodar) sawdust, often referred to as DS, which underwent a sequence of thermochemical pretreatment, enzymatic hydrolysis, and fermentation to produce bioethanol. A overall reducing sugar (TRS) amount of 29.20 g/L was attained following 48 hours omass for both xylanase and cellulase and xylanase enzyme loading of 9 U/g pH 5.0 and a temperature of 30 °C, [144]. Various strategies have been explored to overcome these challenges and increase the profitability of enzymatic hydrolysis [145]. The enzymatic hydrolysis of cellulose is an intricate process driven by the coordinated action of multiple enzymes with distinct modes of operation, commonly found in fungal type apecies like Trichoderma reesei ,Penicillium verruculosum, Sporotrichum Thermophile and Aspergillus niger [146]. The efficiency of enzymatic hydrolysis is closely tied to the chemical and structural attributes of the biomaterial. Key factors include cellulose crystallinity, degree of polymerization (DP), lignin and hemicellulose content and distribution, particle size, and accessible surface area. Traditionally three cellulose activities are recognized. cellobiohydrolases (endoglucanases), which, particularly in amorphous regions, catalyze the random cleavage of cellulose chains; and -glucosidases, which catalyze the hydrolysis of the liberated cello-oligomers to glucose. Beyond glycosyl hydrolases, recent findings propose that oxidative enzymes, specifically lytic polysaccharide mono-oxygenases (LPMOs), also contribute to the overall cellulose degradation process. The ideal circumstances for releasing the most reducing sugars and producing the highest yield of cellulose hydrolysis were 9.07% in substrate and 21.36 FPU/gDM of enzyme loaded for 72 hours. [147]. The addition of PEG has been shown to facilitate enzymatic hydrolysis hence, great concentrations of enxyme are accessible for the breakdown of cellulose [148]. Sawdust from Ayous (Triplochiton scleroxylon) comprises a cellulose content of 53.2 ± 0.3% A loading of 9.07% in substrate related with a loading of 21.36 FPU/gDM of enzyme for 72 hrs established the optimal settings allowing the release of the utmost quantity of reducing sugars and an ultimate yield of hydrolysis of celluloses [149].
2.3. Fermentation process :
In industrial pattern, fermentation is define as any pathway through which feedstocks are converted into desire products via the help of specific strains of microorganisms. According to Louis Pasteur who once described this pathway, that growing microorganisms brought transformation without oxygen or air [150]. Fermentation processes by any raw material that has sugar can produce ethanol. The different feedstocks utilized in the production of ethanol through fermentation processes are mainly categorized into three categories of feedstocks which include ; cellulose , sugars, and starches materials [151].
However, fermentation being a natural process, so for the production of ethanol (or several other various products) from fermentable sugars require microorganisms . Traditionally, Ethanol production depends upon some factors throughout the fermentation pathway which are ethanol, temperature, productions produced during the pretreatment process, and also osmotic stress thereupon some suitable strains are required [152]. Utilization of robust industrial host strains for glucose fermentation can raise ethanol yield because of its strong specific alcohol productivity. These strains are Zymomonas mobilis and Saccharomyces cerevisiae, despite the fact these strains cannot ferment pentoses. Therefore, pentose utilizing yeasts include Candida shehatae, Scheffersomyces stipitisa, and Pachysolen tannophilus [148]. These are known as the most promising strains for ethanol production by different lignocellulosic raw materials, even in co-culture, or in mono-culture. Co-culturing have more benefits than mono-cultures , the co-culturing of S. Cerevisiae with P. stipitis is seems to be more efficient because the both species have similar culturing needs for ideal fermentation [153 ].
Furthermore, depending on lignocellulosic feedstocks and active properties of microorganisms being used, fermentation culture can be perform as a fed batch, batch and continuous process.In the continuous process, substance having feed and culture medium are added continuously in the reactor, that has functional microorganisms. The batch process is a uncomplicated process and is an isolated culture environment in which nutrient amount is limited initially. In this type of system micro-organisms are inoculated that do the fermentation.The Fed-batch process is much utilize in commercial usages for that reason it has more benefits over both of them batch and continuous processes .Workable cells concentration can raise via the fed-batch process, used culture’s lifetime can boost and can increase the product quantity [154].
Two methods are widely employed in fermentation which are separate hydrolysis and fermentation and simultaneous hydrolysis and fermentation. The both methods follow similar steps and can be distinguished just by saccharification weather it is being perform separately or simultaneously from fermentation. In 1991, As per Walter and Schell (SSF) is a better pathway obtaining ethanol from cellluose enzymatically [150]. In the SSF process, both saccharification and fermentation are carried out within the same reactor, therefore together yeast and cellulase enzyme decrease the accumulation or concentration of sugars in the reactor. Thus, raise the rate of saccharification and yield [155]. 4.74% ethanol can be produce in 72 h via SHF method while 6.05% ethanol can be produce via SSF method in 24 h [156]. In SSF method, the growing yeast require low temperature so that the optimal temperature needed for hydrolysis is compromised [157]. Moreover, the cost of production of ethanol via SHF method is seem to be higher than that of SSF method by 11 % [158]. but this method has one disadvantage, the conditions for both fermentation and enzymatic saccharification should be similar [159].
Table 4. shows the fermentation methods
Fermentation | SSF | SHF |
Strains | Zymomonas mobilis and Saccharomyces cerevisiae | Zymomonas mobilis and Saccharomyces cerevisiae |
Tempreture | Low temperature | Needs higher temperature than ssf |
Time | 24 h | 72 h |
Yield | 6.05% | 4.74% |
2.4. Distillation process :
The ethanol mixture achieved from fermentation method require to be again processed in order to eliminate water content [160]. Throughout distillation, ethanol is extracted from the mixture of other components. Various separation processes can be utilized such as, extractive distillation, azeotropic distillation, ordinary distillation, liquid extraction fermentation hybrid, membrane separation and absorption. Through the ordinary distillation method 96% ethanol can be recover but, to obtain 99.8% of ethanol (anhydrous ethanol), dehydration is required ahead [161]. Before, dehydration was mostly done via azeotropic distillation. Because of high energy claim, azeotropic distillation was substituted by adsorption in respect to zeolite molecular sieves [162].
Figure 5. Overall processes of bioethanol production via sawdust
3. Conclusion:
In this paper it is concluded that, bioethanol is one of the most promising renewable energies with a strong potential to replace fossil fuels. Moreover, bioethanol production from locally available sawdust is feasible. The production of bioethanol from sawdust involves several pretreatment methods to enhance the effectiveness of enzymatic hydrolysis and subsequent fermentation processes. Sawdust, a lignocellulosic biomass, contains hemicellulose, cellulose and lignin. Pretreatment is essential to degrade the complex shape of these components and make them more accessible for enzymatic conversion. Common pretreatment methods comprise physical methods like milling and grinding, chemical methods such as acid or alkaline treatment, physiochemical processes such as steam explosion,liquid hot water,ammonia fiber explosion and co2 explosion and biological methods using fungi or bacteria. Each method aims to remove or modify lignin, interrupt into the crystalline shape of cellulose, and solubilize hemicellulose. These pretreatment steps improve the total yield of fermentable sugars during enzymatic hydrolysis. The predigested sawdust is then accounted to enzymatic hydrolysis to degrade cellulose into fermentable sugars, followed by fermentation to produce bioethanol. The selection of an optimal pretreatment method depends on factors such as the feedstock characteristics, economic viability, and environmental considerations, as the efficient conversion of sawdust into bioethanol is crucial for sustainable and environmentally friendly biofuel production.
3.1. Future prospective :
Numerous microorganisms have been used for fermentation of sugars however, the best microorganism (can efficiently ferment together pentose plus hexoses) does not exist yet. Further investigation is needed.
Different chemical pretreatment methods are developed which show positive impact on breaking down of lignocellulose but, some of them are expensive and not eco-friendly therefore further research is required to develop ideal pretreatment methods.
Reference:
3. Alvarez, C.E.S., et al., Alkaline pretreatment of Mexican pine residues for bioethanol production. African Journal of Biotechnology, 2013. 12(31).
4. Anca-Couce, A. and I. Obernberger, Application of a detailed biomass pyrolysis kinetic scheme to hardwood and softwood torrefaction. Fuel, 2016. 167: p. 158-167.
5. Gao, H., et al., Combined steam explosion and optimized green-liquor pretreatments are effective for complete saccharification to maximize bioethanol production by reducing lignocellulose recalcitrance in one-year-old bamboo. Renewable Energy, 2021. 175: p. 1069-1079.
6. Le Tan, N.T., et al., The combination of acidic and alkaline pretreatment for a lignocellulose material in simultaneous saccharification and fermentation (SSF) process. Chemical Engineering Transactions, 2021. 89: p. 43-48.
7. Gebrehiwot, G., S.A. Jabasingh, and A. Yimam, Production of cellulosic ethanol from wood sawdust by sulphuric acid hydrolysis. Journal of Petroleum Engineering & Technology, 7 (3), 30, 2017. 35.
8. Alio, M.A., et al., Modeling and simulation of a sawdust mixture-based integrated biorefinery plant producing bioethanol. Bioresource technology, 2021. 325: p. 124650.
9. Anggraeni, S., et al., Effects of particle size and composition of sawdust/carbon from rice husk on the briquette performance. J. Eng. Sci. Technol, 2021. 16(3): p. 2298-2311.
10. Ahmad, Z.S., M. Munaim, and F.M. Said. Characterization of meranti wood sawdust and removal of lignin content using pre-treatment process. in Proceedings of the National Conference for Postgraduate Research (NCON-PGR 2016). 2016.
11. Yildirim, O., et al., Statistical optimization of dilute acid pretreatment of lignocellulosic biomass by response surface methodology to obtain fermentable sugars for bioethanol production. International Journal of Energy Research, 2021. 45(6): p. 8882-8899.
12. Puligundla, P., S.-E. Oh, and C. Mok, Microwave-assisted pretreatment technologies for the conversion of lignocellulosic biomass to sugars and ethanol: a review. Carbon letters, 2016. 17(1): p. 1-10.
13. Rochón, E., et al., Co-production of bioethanol and xylosaccharides from steam-exploded eucalyptus sawdust using high solid loads in enzymatic hydrolysis: Effect of alkaline impregnation. Industrial Crops and Products, 2022. 175: p. 114253.
14. Sindhu, R., et al., Dilute acid pretreatment and enzymatic saccharification of sugarcane tops for bioethanol production. Bioresource Technology, 2011. 102(23): p. 10915-10921.
15. Afzal, A., et al., Bioethanol production from saw dust through simultaneous saccharification and fermentation. Punjab University Journal of Zoology, 2018. 33(2): p. 145-148.
16. Mosier, N., et al., Features of promising technologies for pretreatment of lignocellulosic biomass. Bioresource technology, 2005. 96(6): p. 673-686.
17. Dziekońska-Kubczak, U.A., et al., Comparison of steam explosion, dilute acid, and alkali pretreatments on enzymatic saccharification and fermentation of hardwood sawdust. BioResources, 2018. 13(3): p. 6970-6984.
18. Farías-Sánchez, J.C., et al., Simultaneous saccharification and fermentation of pine sawdust (Pinus pseudostrobus L.) pretreated with nitric acid and sodium hydroxide for bioethanol production. BioResources, 2017. 12(1): p. 1052-1063.
19. Kim, J.K., et al., Statistical optimization of enzymatic saccharification and ethanol fermentation using food waste. Process Biochemistry, 2008. 43(11): p. 1308-1312.
20. Shukla, A., et al., Strategies of pretreatment of feedstocks for optimized bioethanol production: distinct and integrated approaches. Biotechnology for Biofuels and Bioproducts, 2023. 16(1): p. 44.
21. Shahbazi, A. and B. Zhang, Dilute and concentrated acid hydrolysis of lignocellulosic biomass. Bioalcohol production, 2010: p. 143-158.
22. Lee, Y., Z. Wu, and R. Torget, Modeling of countercurrent shrinking-bed reactor in dilute-acid total-hydrolysis of lignocellulosic biomass. Bioresource Technology, 2000. 71(1): p. 29-39.
23. Bravo, C., et al., Selective arabinose extraction from Pinus sp. sawdust by two-step soft acid hydrolysis. Industrial Crops and Products, 2017. 104: p. 229-236.
24. Tulashie, S.K., et al., Acid hydrolysis of sawdust waste into bioethanol. Biomass Conversion and Biorefinery, 2023. 13(7): p. 5743-5756.
25. Tulashie, S.K., et al., Acid hydrolysis of sawdust waste into bioethanol. Biomass Conversion and Biorefinery, 2021: p. 1-14.
26. Kim, J.S., Y. Lee, and T.H. Kim, A review on alkaline pretreatment technology for bioconversion of lignocellulosic biomass. Bioresource technology, 2016. 199: p. 42-48.
27. Trevorah, R.M. and M.Z. Othman, Alkali pretreatment and enzymatic hydrolysis of Australian timber mill sawdust for biofuel production. Journal of Renewable Energy, 2015. 2015.
28. Mesa, L., et al., The effect of organosolv pretreatment variables on enzymatic hydrolysis of sugarcane bagasse. Chemical Engineering Journal, 2011. 168(3): p. 1157-1162.
29. Amiri, H., K. Karimi, and H. Zilouei, Organosolv pretreatment of rice straw for efficient acetone, butanol, and ethanol production. Bioresource technology, 2014. 152: p. 450-456.
30. Meng, X., et al., Effects of the advanced organosolv pretreatment strategies on structural properties of woody biomass. Industrial crops and products, 2020. 146: p. 112144.
31. Sannigrahi, P., S.J. Miller, and A.J. Ragauskas, Effects of organosolv pretreatment and enzymatic hydrolysis on cellulose structure and crystallinity in Loblolly pine. Carbohydrate research, 2010. 345(7): p. 965-970.
32. Goh, C.S., et al., Evaluation and optimization of organosolv pretreatment using combined severity factors and response surface methodology. Biomass and bioenergy, 2011. 35(9): p. 4025-4033.
33. Chum, H.L., D.K. Johnson, and S.K. Black, Organosolv pretreatment for enzymic hydrolysis of poplars. 2. Catalyst effects and the combined severity parameter. Industrial & engineering chemistry research, 1990. 29(2): p. 156-162.
34. Araque, E., et al., Evaluation of organosolv pretreatment for the conversion of Pinus radiata D. Don to ethanol. Enzyme and Microbial Technology, 2008. 43(2): p. 214-219.
35. Park, N., et al., Organosolv pretreatment with various catalysts for enhancing enzymatic hydrolysis of pitch pine (Pinus rigida). Bioresource technology, 2010. 101(18): p. 7046-7053.
36. Moniruzzaman, M. and M. Goto, Ionic liquid pretreatment of lignocellulosic biomass for enhanced enzymatic delignification. Application of ionic liquids in Biotechnology, 2019: p. 61-77.
37. Zhang, J., et al., Recent developments in ionic liquid pretreatment of lignocellulosic biomass for enhanced bioconversion. Sustainable Energy & Fuels, 2021. 5(6): p. 1655-1667.
38. Gschwend, F.J., et al., Pretreatment of lignocellulosic biomass with low-cost ionic liquids. JoVE (Journal of Visualized Experiments), 2016(114): p. e54246.
39. Luo, J., M. Cai, and T. Gu, Pretreatment of lignocellulosic biomass using green ionic liquids. Green biomass pretreatment for biofuels production, 2013: p. 127-153.
40. Farahani, S.V., Y.-W. Kim, and C.A. Schall, A coupled low temperature oxidative and ionic liquid pretreatment of lignocellulosic biomass. Catalysis Today, 2016. 269: p. 2-8.
41. Mankar, A.R., et al., Pretreatment of lignocellulosic biomass: A review on recent advances. Bioresource Technology, 2021. 334: p. 125235.
42. Aftab, M.N., et al., Different pretreatment methods of lignocellulosic biomass for use in biofuel production. Biomass for bioenergy-recent trends and future challenges, 2019: p. 1-24.
43. Bhutto, A.W., et al., Insight into progress in pre-treatment of lignocellulosic biomass. Energy, 2017. 122: p. 724-745.
44. Mood, S.H., et al., Lignocellulosic biomass to bioethanol, a comprehensive review with a focus on pretreatment. Renewable and sustainable energy reviews, 2013. 27: p. 77-93.
45. Che Kamarludin, S.N., et al., Mechanical pretreatment of lignocellulosic biomass for biofuel production. Applied Mechanics and Materials, 2014. 625: p. 838-841.
46. Zhang, M., et al., Biofuel manufacturing from woody biomass: effects of sieve size used in biomass size reduction. BioMed Research International, 2012. 2012.
47. Potumarthi, R., R.R. Baadhe, and S. Bhattacharya, Fermentable sugars from lignocellulosic biomass: technical challenges, in Biofuel technologies: recent developments. 2013, Springer. p. 3-27.
48. Moiceanu, G., et al., Energy consumption at size reduction of lignocellulose biomass for bioenergy. Sustainability, 2019. 11(9): p. 2477.
49. Arce, C. and L. Kratky, Mechanical pretreatment of lignocellulosic biomass towards enzymatic/fermentative valorization. Iscience, 2022.
50. Barakat, A., et al., Mechanical pretreatments of lignocellulosic biomass: towards facile and environmentally sound technologies for biofuels production. Rsc Advances, 2014. 4(89): p. 48109-48127.
51. Jewiarz, M., et al., Impact of the drying temperature and grinding technique on biomass grindability. Energies, 2020. 13(13): p. 3392.
52. Hoang, A.T., et al., Insight into the recent advances of microwave pretreatment technologies for the conversion of lignocellulosic biomass into sustainable biofuel. Chemosphere, 2021. 281: p. 130878.
53. Dahadha, S., et al., Evaluation of different pretreatment processes of lignocellulosic biomass for enhanced biomethane production. Energy & Fuels, 2017. 31(10): p. 10335-10347.
54. Laghari, S.M., M.H. Isa, and H. Saleem, Microwave individual and combined pre-treatments on lignocellulosic biomasses. IOSR J. Eng., 2014. 4(2): p. 14-28.
55. Pellera, F.-M. and E. Gidarakos, Microwave pretreatment of lignocellulosic agroindustrial waste for methane production. Journal of environmental chemical engineering, 2017. 5(1): p. 352-365.
56. Rezania, S., et al., Different pretreatment technologies of lignocellulosic biomass for bioethanol production: An overview. Energy, 2020. 199: p. 117457.
57. Mikulski, D. and G. Kłosowski, Cellulose hydrolysis and bioethanol production from various types of lignocellulosic biomass after microwave-assisted hydrotropic pretreatment. Renewable Energy, 2023. 206: p. 168-179.
58. Saha, B.C., A. Biswas, and M.A. Cotta, Microwave pretreatment, enzymatic saccharification and fermentation of wheat straw to ethanol. Journal of Biobased Materials and Bioenergy, 2008. 2(3): p. 210-217.
59. Kannan, T.S., A. Ahmed, and A. Farid Nasir, Energy efficient microwave irradiation of sago bark waste (SBW) for bioethanol production. Advanced Materials Research, 2013. 701: p. 249-253.
60. Richel, A. and N. Jacquet, Microwave-assisted thermochemical and primary hydrolytic conversions of lignocellulosic resources: a review. Biomass Conversion and Biorefinery, 2015. 5: p. 115-124.
61. Keshwani, D.R., et al. Microwave pretreatment of switchgrass to enhance enzymatic hydrolysis. in 2007 ASAE Annual Meeting. 2007. American Society of Agricultural and Biological Engineers.
62. Li, H., et al., Microwave irradiation–A green and efficient way to pretreat biomass. Bioresource technology, 2016. 199: p. 34-41.
63. Tian, S.-Q., R.-Y. Zhao, and Z.-C. Chen, Review of the pretreatment and bioconversion of lignocellulosic biomass from wheat straw materials. Renewable and Sustainable Energy Reviews, 2018. 91: p. 483-489.
64. Ethaib, S., et al., Microwave-assisted dilute acid pretreatment and enzymatic hydrolysis of sago palm bark. BioResources, 2016. 11(3): p. 5687-5702.
65. Sasaki, C., et al., Microwave-assisted glucose production from bode (Styrax tonkinensis) woody biomass for bioethanol production. Journal of Material Cycles and Waste Management, 2019. 21: p. 201-204.
66. Marx, S., et al., Fuel ethanol production from sweet sorghum bagasse using microwave irradiation. Biomass and Bioenergy, 2014. 65: p. 145-150.
67. Chaturvedi, V. and P. Verma, An overview of key pretreatment processes employed for bioconversion of lignocellulosic biomass into biofuels and value added products. 3 Biotech, 2013. 3: p. 415-431.
68. Han, S.-Y., et al., Extrusion process to enhance the pretreatment effect of ionic liquid for improving enzymatic hydrolysis of lignocellulosic biomass. Wood Science and Technology, 2020. 54: p. 599-613.
69. Ravindran, R. and A.K. Jaiswal, A comprehensive review on pre-treatment strategy for lignocellulosic food industry waste: challenges and opportunities. Bioresource technology, 2016. 199: p. 92-102.
70. Maurya, D.P., A. Singla, and S. Negi, An overview of key pretreatment processes for biological conversion of lignocellulosic biomass to bioethanol. 3 Biotech, 2015. 5: p. 597-609.
71. Konan, D., et al., An Overview of Extrusion as a Pretreatment Method of Lignocellulosic Biomass. Energies, 2022. 15(9): p. 3002.
72. Zheng, J. and L. Rehmann, Extrusion pretreatment of lignocellulosic biomass: a review. International journal of molecular sciences, 2014. 15(10): p. 18967-18984.
73. Lamsal, B., et al., Extrusion as a thermo-mechanical pre-treatment for lignocellulosic ethanol. Biomass and Bioenergy, 2010. 34(12): p. 1703-1710.
74. Liu, C., et al., Alkaline twin-screw extrusion pretreatment for fermentable sugar production. Biotechnology for biofuels, 2013. 6: p. 1-11.
75. Taherzadeh, M.J. and K. Karimi, Pretreatment of lignocellulosic wastes to improve ethanol and biogas production: a review. International journal of molecular sciences, 2008. 9(9): p. 1621-1651.
76. Zhuang, X., et al., Liquid hot water pretreatment of lignocellulosic biomass for bioethanol production accompanying with high valuable products. Bioresource technology, 2016. 199: p. 68-75.
77. Capolupo, L. and V. Faraco, Green methods of lignocellulose pretreatment for biorefinery development. Applied microbiology and biotechnology, 2016. 100: p. 9451-9467.
78. Jacquet, N., et al., Application of steam explosion as pretreatment on lignocellulosic material: a review. Industrial & Engineering Chemistry Research, 2015. 54(10): p. 2593-2598.
79. Focher, B., et al., Steam exploded biomass for the preparation of conventional and advanced biopolymer-based materials. Biomass and Bioenergy, 1998. 14(3): p. 187-194.
80. Baêta, B.E.L., et al., Steam explosion pretreatment improved the biomethanization of coffee husks. Bioresource Technology, 2017. 245: p. 66-72.
81. Hoang, A.T., et al., Steam explosion as sustainable biomass pretreatment technique for biofuel production: Characteristics and challenges. Bioresource technology, 2023: p. 129398.
82. Li, J., G. Henriksson, and G. Gellerstedt, Lignin depolymerization/repolymerization and its critical role for delignification of aspen wood by steam explosion. Bioresource technology, 2007. 98(16): p. 3061-3068.
83. Stelte, W., Steam explosion for biomass pre-treatment. Danish Technological Institute, 2013: p. 1-15.
84. Ziegler-Devin, I., L. Chrusciel, and N. Brosse, Steam explosion pretreatment of lignocellulosic biomass: a mini-review of theorical and experimental approaches. Frontiers in Chemistry, 2021. 9: p. 705358.
85. Periyasamy, S., et al., Chemical, physical and biological methods to convert lignocellulosic waste into value-added products. A review. Environmental Chemistry Letters, 2022. 20(2): p. 1129-1152.
86. Gu, X., et al., Thermal behavior and kinetics of the pyrolysis of the raw/steam exploded poplar wood sawdust. Journal of Analytical and Applied Pyrolysis, 2014. 106: p. 177-186.
87. Muzamal, M., et al., Structural changes in spruce wood during different steps of steam explosion pretreatment. Holzforschung, 2015. 69(1): p. 61-66.
88. Akizuki, S., et al., Impacts of steam explosion pretreatment on semi-continuous anaerobic digestion of lignin-rich submerged macrophyte. Journal of Cleaner Production, 2023. 385: p. 135377.
89. Borrero-López, A., et al., Modelling the reactions of cellulose, hemicellulose and lignin submitted to hydrothermal treatment. Industrial Crops and Products, 2018. 124: p. 919-930.
90. Schütt, F., J. Puls, and B. Saake, Optimization of steam pretreatment conditions for enzymatic hydrolysis of poplar wood: 11th EWLP, Hamburg, Germany, August 16–19, 2010. 2011.
91. Santo, M.C.E., et al., Physical techniques shed light on the differences in sugarcane bagasse structure subjected to steam explosion pretreatments at equivalent combined severity factors. Industrial Crops and Products, 2020. 158: p. 113003.
92. Brownell, H., E. Yu, and J. Saddler, Steam‐explosion pretreatment of wood: Effect of chip size, acid, moisture content and pressure drop. Biotechnology and bioengineering, 1986. 28(6): p. 792-801.
93. Negro, M., et al., Changes in various physical/chemical parameters of Pinus pinaster wood after steam explosion pretreatment. Biomass and bioenergy, 2003. 25(3): p. 301-308.
94. Shimizu, K., et al., Integrated process for total utilization of wood components by steam-explosion pretreatment. Biomass and Bioenergy, 1998. 14(3): p. 195-203.
95. Grethlein, H.E. and A.O. Converse, Common aspects of acid prehydrolysis and steam explosion for pretreating wood. Bioresource technology, 1991. 36(1): p. 77-82.
96. Grous, W.R., A.O. Converse, and H.E. Grethlein, Effect of steam explosion pretreatment on pore size and enzymatic hydrolysis of poplar. Enzyme and Microbial technology, 1986. 8(5): p. 274-280.
97. Biswas, A.K., et al., Change of pyrolysis characteristics and structure of woody biomass due to steam explosion pretreatment. Fuel processing technology, 2011. 92(10): p. 1849-1854.
98. Xu, Z. and F. Huang, Pretreatment methods for bioethanol production. Applied biochemistry and biotechnology, 2014. 174: p. 43-62.
99. Chen, W.-H., et al., Liquid hot water as sustainable biomass pretreatment technique for bioenergy production: A review. Bioresource technology, 2022. 344: p. 126207.
100. Imman, S., et al., Optimization of sugar recovery from pineapple leaves by acid-catalyzed liquid hot water pretreatment for bioethanol production. Energy Reports, 2021. 7: p. 6945-6954.
101. Yang, H., et al., Bioethanol production from bamboo with alkali-catalyzed liquid hot water pretreatment. Bioresource technology, 2019. 274: p. 261-266.
102. Wang, W., et al., Combination of biological pretreatment with liquid hot water pretreatment to enhance enzymatic hydrolysis of Populus tomentosa. Bioresource technology, 2012. 107: p. 282-286.
103. Ko, J.K., et al., Effect of liquid hot water pretreatment severity on properties of hardwood lignin and enzymatic hydrolysis of cellulose. Biotechnology and bioengineering, 2015. 112(2): p. 252-262.
104. Martín-Lara, M., et al., Liquid hot water pretreatment and enzymatic hydrolysis as a valorization route of Italian green pepper waste to delivery free sugars. Foods, 2020. 9(11): p. 1640.
105. Cara, C., et al., Influence of solid loading on enzymatic hydrolysis of steam exploded or liquid hot water pretreated olive tree biomass. Process Biochemistry, 2007. 42(6): p. 1003-1009.
106. Nitsos, C.K., et al., Optimization of hydrothermal pretreatment of hardwood and softwood lignocellulosic residues for selective hemicellulose recovery and improved cellulose enzymatic hydrolysis. ACS Sustainable Chemistry & Engineering, 2016. 4(9): p. 4529-4544.
107. Latif, A.A., et al., Ammonia-based pretreatment for ligno-cellulosic biomass conversion–an overview. Journal of Engineering Science and Technology, 2018. 13(6): p. 1595-1620.
108. Mussatto, S.I., Biomass fractionation technologies for a lignocellulosic feedstock based biorefinery. 2016: Elsevier.
109. Chundawat, S.P., et al., Ammonia fiber expansion (AFEX) pretreatment of lignocellulosic biomass. Journal of visualized experiments, 2020(158).
110. Lee, J.M., H. Jameel, and R.A. Venditti, A comparison of the autohydrolysis and ammonia fiber explosion (AFEX) pretreatments on the subsequent enzymatic hydrolysis of coastal Bermuda grass. Bioresource Technology, 2010. 101(14): p. 5449-5458.
111. Mathew, A.K., et al., An evaluation of dilute acid and ammonia fiber explosion pretreatment for cellulosic ethanol production. Bioresource Technology, 2016. 199: p. 13-20.
112. Zhao, C., Q. Shao, and S.P. Chundawat, Recent advances on ammonia-based pretreatments of lignocellulosic biomass. Bioresource technology, 2020. 298: p. 122446.
113. Brodeur, G., et al., Chemical and physicochemical pretreatment of lignocellulosic biomass: a review. Enzyme research, 2011. 2011.
114. Chundawat, S.P., et al., Multifaceted characterization of cell wall decomposition products formed during ammonia fiber expansion (AFEX) and dilute acid based pretreatments. Bioresource technology, 2010. 101(21): p. 8429-8438.
115. Aditiya, H., et al., Second generation bioethanol production: A critical review. Renewable and sustainable energy reviews, 2016. 66: p. 631-653.
116. Talaiekhozani, A. and S. Rezania, A critical review on the various pretreatment technologies of lignocellulosic materials. Journal of Environmental Treatment Techniques, 2020. 8(3): p. 925-935.
117. Mahmud, N. and K.A. Rosentrater, Low Moisture Anhydrous Ammonia Pretreatment of Four Lignocellulosic Materials—Distillers Dried Grains With Solubles, Corn Gluten Feed, Corn Fiber, and Oil Palm Frond. Frontiers in Energy Research, 2021. 9: p. 682522.
118. Alizadeh, H., et al., Pretreatment of switchgrass by ammonia fiber explosion (AFEX). Applied biochemistry and biotechnology, 2005. 124: p. 1133-1141.
119. Teymouri, F., et al., Optimization of the ammonia fiber explosion (AFEX) treatment parameters for enzymatic hydrolysis of corn stover. Bioresource technology, 2005. 96(18): p. 2014-2018.
120. Campbell, T., et al., Scale‐up and operation of a pilot‐scale ammonia fiber expansion reactor. Biotechnology and Bioengineering, 2020. 117(4): p. 1241-1246.
121. Morais, A.R., A.M. da Costa Lopes, and R. Bogel-Łukasik, Carbon dioxide in biomass processing: contributions to the green biorefinery concept. Chemical reviews, 2015. 115(1): p. 3-27.
122. Medina-Gonzalez, Y., S. Camy, and J.-S. Condoret, Cellulosic materials as biopolymers and supercritical CO2 as a green process: chemistry and applications. International Journal of Sustainable Engineering, 2012. 5(1): p. 47-65.
123. Zheng, Y., H.M. Lin, and G.T. Tsao, Pretreatment for cellulose hydrolysis by carbon dioxide explosion. Biotechnology progress, 1998. 14(6): p. 890-896.
124. Badgujar, K.C., R. Dange, and B.M. Bhanage, Recent advances of use of the supercritical carbon dioxide for the biomass pre-treatment and extraction: A mini-review. Journal of the Indian Chemical Society, 2021. 98(1): p. 100018.
125. Zhang, J., L. Yang, and H. Liu, Green and efficient processing of wood with supercritical CO2: a review. Applied Sciences, 2021. 11(9): p. 3929.
126. Matsunaga, M., et al., A novel method of acetylation of wood using supercritical carbon dioxide. Journal of wood science, 2010. 56(4): p. 293-298.
127. Chen, H., et al., A review on the pretreatment of lignocellulose for high-value chemicals. Fuel Processing Technology, 2017. 160: p. 196-206.
128. Meints, T., et al., Highly effective impregnation and modification of spruce wood with epoxy-functional siloxane using supercritical carbon dioxide solvent. Wood Science and Technology, 2018. 52: p. 1607-1620.
129. Jaxel, J., F.W. Liebner, and C. Hansmann, Solvent-free dyeing of solid wood in water-saturated supercritical carbon dioxide. ACS Sustainable Chemistry & Engineering, 2020. 8(14): p. 5446-5451.
130. Manosroi, A., et al., Characteristics of niosomes prepared by supercritical carbon dioxide (scCO2) fluid. International journal of pharmaceutics, 2008. 352(1-2): p. 248-255.
131. Rahim, E., et al., Experimental investigation of supercritical carbon dioxide (SCCO2) performance as a sustainable cooling technique. Procedia Cirp, 2016. 40: p. 637-641.
132. Long, J.-J., et al., Effect of treatment pressure on wool fiber in supercritical carbon dioxide fluid. Journal of cleaner production, 2013. 43: p. 52-58.
133. Azhar, S.H.M., et al., Yeasts in sustainable bioethanol production: A review. Biochemistry and biophysics reports, 2017. 10: p. 52-61.
134. Sindhu, R., P. Binod, and A. Pandey, Biological pretreatment of lignocellulosic biomass–An overview. Bioresource technology, 2016. 199: p. 76-82.
135. Poszytek, K., et al., Microbial consortium with high cellulolytic activity (MCHCA) for enhanced biogas production. Frontiers in Microbiology, 2016. 7: p. 324.
136. Indrasith, L., T. Sasaki, and O. Yamashita, A unique protease responsible for selective degradation of a yolk protein in Bombyx mori. Purification, characterization, and cleavage profile. Journal of Biological Chemistry, 1988. 263(2): p. 1045-1051.
137. Lass, A., et al., Lipolysis–a highly regulated multi-enzyme complex mediates the catabolism of cellular fat stores. Progress in lipid research, 2011. 50(1): p. 14-27.
138. Pandey, A., et al., Efficient microorganism for bioethanol production from Lignocellulosic Azolla. Research Journal of Environmental Sciences, 2014. 8(6): p. 350.
139. Millati, R., et al., Biological pretreatment of lignocelluloses with white-rot fungi and its applications: a review. BioResources, 2011. 6(4): p. 5224-5259.
140. Ummalyma, S.B., et al., Biological pretreatment of lignocellulosic biomass—Current trends and future perspectives, in Second and third generation of feedstocks. 2019, Elsevier. p. 197-212.
141. Kumar, P., et al., Methods for pretreatment of lignocellulosic biomass for efficient hydrolysis and biofuel production. Industrial & engineering chemistry research, 2009. 48(8): p. 3713-3729.
142. Kucharska, K., et al., Pretreatment of lignocellulosic materials as substrates for fermentation processes. Molecules, 2018. 23(11): p. 2937.
143. Luo, X., et al., Promoting enzymatic hydrolysis of lignocellulosic biomass by inexpensive soy protein. Biotechnology for biofuels, 2019. 12(1): p. 1-13.
144. Yang, B., et al., Enzymatic hydrolysis of cellulosic biomass. Biofuels, 2011. 2(4): p. 421-449.
145. Rocha-Martín, J., et al., Additives enhancing enzymatic hydrolysis of lignocellulosic biomass. Bioresource Technology, 2017. 244: p. 48-56.
146. Fenila, F. and Y. Shastri, Optimal control of enzymatic hydrolysis of lignocellulosic biomass. Resource-Efficient Technologies, 2016. 2: p. S96-S104.
147. Wahlström, R. and A. Suurnäkki, Enzymatic hydrolysis of lignocellulosic polysaccharides in the presence of ionic liquids. Green Chemistry, 2015. 17(2): p. 694-714.
148. Vasić, K., Ž. Knez, and M. Leitgeb, Bioethanol production by enzymatic hydrolysis from different lignocellulosic sources. Molecules, 2021. 26(3): p. 753.
149. Assabjeu, A.C., et al., Optimization of the enzymatic hydrolysis of cellulose of triplochiton scleroxylon sawdust in view of the production of bioethanol. Scientific African, 2020. 8: p. e00438.
150. Otulugbu, K., Production of ethanol from cellulose (sawdust). 2012.
151. Lin, Y., S.J.A.m. Tanaka, and biotechnology, Ethanol fermentation from biomass resources: current state and prospects. 2006. 69: p. 627-642.
152. Doğan, A., et al., Improvements of tolerance to stress conditions by genetic engineering in Saccharomyces cerevisiae during ethanol production. 2014. 174: p. 28-42.
153. Ben Atitallah, I., et al., A Comparative Study of Various Pretreatment Approaches for Bio-Ethanol Production from Willow Sawdust, Using Co-Cultures and Mono-Cultures of Different Yeast Strains. 2022. 27(4): p. 1344.
154. Vasić, K., Ž. Knez, and M.J.M. Leitgeb, Bioethanol production by enzymatic hydrolysis from different lignocellulosic sources. 2021. 26(3): p. 753.
155. Lin, Y.-S., et al., Ethanol production by simultaneous saccharification and fermentation in rotary drum reactor using thermotolerant Kluveromyces marxianus. 2013. 105: p. 389-394.
156. Dahnum, D., et al., Comparison of SHF and SSF processes using enzyme and dry yeast for optimization of bioethanol production from empty fruit bunch. 2015. 68: p. 107-116.
157. Kadhum, H.J., D.M. Mahapatra, and G.S.J.B.t. Murthy, A comparative account of glucose yields and bioethanol production from separate and simultaneous saccharification and fermentation processes at high solids loading with variable PEG concentration. 2019. 283: p. 67-75.
158. Wingren, A., M. Galbe, and G.J.B.p. Zacchi, Techno‐economic evaluation of producing ethanol from softwood: Comparison of SSF and SHF and identification of bottlenecks. 2003. 19(4): p. 1109-1117.
159. Ask, M., et al., Challenges in enzymatic hydrolysis and fermentation of pretreated Arundo donax revealed by a comparison between SHF and SSF. 2012. 47(10): p. 1452-1459.
160. Sebayang, A., et al., A perspective on bioethanol production from biomass as alternative fuel for spark ignition engine. Rsc Advances, 2016. 6(18): p. 14964-14992.
161. Rocha-Meneses, L., et al., Second-generation bioethanol production: A review of strategies for waste valorisation. 2017. 15(3): p. 830-847.
162. Branco, R.H., L.S. Serafim, and A.M.J.F. Xavier, Second generation bioethanol production: on the use of pulp and paper industry wastes as feedstock. 2018. 5(1): p. 4.
[1] Correspondence to Dr. Muhammad Haroon, E-mail: Muhammad.haroon@uot.edu.pk
For reading on other academic topics like the Biological perspective of Education and the Philosophical perspective of Education.